Why Make Cold Iron Ore and By-product Briquettes
With the shortage of iron ore resources, the accumulation of various metallurgical wastes, and the environmental pollution issues associated with steel production, the utilization of low-grade iron ore and iron- and carbon-containing by-products has become a crucial breakthrough in addressing these problems. However, due to the influence of raw material particle size, composition, and various process characteristics, the application of these iron-containing wastes in blast furnace ironmaking is limited. To protect the environment and efficiently utilize resources, some of these iron-containing wastes are used to replace part of the iron ore fines in the sintering process to produce sinter. However, the presence of harmful elements (zinc, potassium, sodium) in some iron-containing wastes limits their use in sinter production.
Cold briquetting is increasingly favored for its advantages in recycling blast furnace secondary resources, agglomeration, and energy conservation and emission reduction.
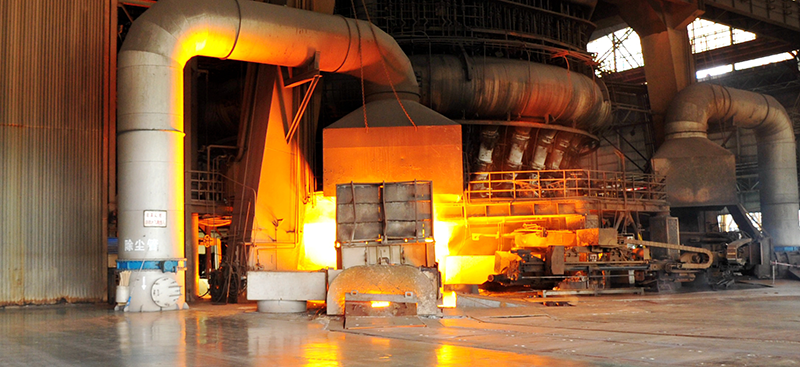
By mixing various iron-containing wastes with binders and molding them as smelting raw materials used in blast furnaces, electric arc furnaces, converters, shaft furnaces, rotary kilns, etc., this not only realizes the recycling of metallurgical secondary resources but also alleviates the environmental pollution pressure caused by solid waste. Compared to traditional agglomeration processes, the cold iron ore and by-product briquette making technology has shorter steps, does not require high-temperature treatment, and reduces the energy consumption in the agglomeration process. Applying such briquettes in blast furnace ironmaking can improve the permeability of the furnace burden to varying degrees, and the presence of carbon in the briquettes can reduce coke consumption during blast furnace ironmaking, saving energy, reducing carbon dioxide and pollutant emissions, and improving overall benefits.
The Process
In 1899, Finland first used fine magnetite powder to produce cold iron ore briquettes for blast furnace smelting operations. However, compared to traditional sintering and pelletizing processes, the equipment for cold iron ore briquettes had lower production efficiency at that time. With the gradual improvement of the briquetting process and the increasing demand for recycling solid waste and green, low-carbon steel production, cold iron ore and by-product briquette making technology has been applied in blast furnace ironmaking.
This process abandons the high-temperature treatment steps in conventional sintering and pelletizing processes. It applies pressure to the mixed materials, destroying the mechanical stress between particles to form an “arch effect” and curing the formed briquettes naturally in the environment. Finally, the briquettes are used as main or auxiliary materials and are charged into the blast furnace or other ironmaking furnaces for smelting. The briquettes are produced from fine powders, allowing their chemical composition to be adjusted according to production requirements to achieve the best quality for furnaces.
3 Types of Briquetting Technology
Cold iron ore and by-product briquette making can be classified into three types based on the forming equipment:
- Roller briquetting technology using roller briquette machines to produce briquettes.
- Vacuum extrusion technology that uses shear stress to briquette mixed materials (compared to roller briquetting, briquettes produced by this technology have higher strength and more uniform density).
- Disc pelletizing to produce iron-containing pellet furnace materials.
The History
From 1899 to the early 1920s, cold iron ore briquette making technology rapidly spread in the field of blast furnace smelting. In the 1960s, Ukraine’s Alchevsk, Russia’s Nizheny Tagil, and Magnitogorsk steel plants used roller briquetting technology to turn iron-containing wastes from steel production into cold by-product briquettes suitable for blast furnace production. In 1993, Bethlehem Steel Corp in the United States successfully constructed a production line using vacuum extrusion technology to produce cold by-product briquettes from metallurgical wastes like oxygen converter sludge and dust, using them as blast furnace charge for ironmaking. Subsequently, BHP Billiton built a 700,000-ton annual capacity cold briquette production line in Colombia for ferronickel production.
To efficiently utilize iron-containing wastes generated during smelting and achieve internal recycling, in 2011, India’s Suraj Products Ltd introduced a vacuum extrusion briquette making production line at a small steel plant to produce cold by-product briquettes with TFe of 46-48%, CaO of 10-11%, SiO2 of 7.2-7.7%, loss on ignition of 11-11.9%, and alkalinity of 1.4. They successfully used these briquettes for ironmaking in a 45m³ small industrial blast furnace with 10%, 80%, and 100% briquette inclusion. They found that as the briquette proportion increased, the coke ratio gradually decreased. When the proportion reached 100%, coke consumption decreased by about 200 kg/t, the hot metal temperature slightly increased, and the pig iron composition was almost the same as using iron ore for smelting.
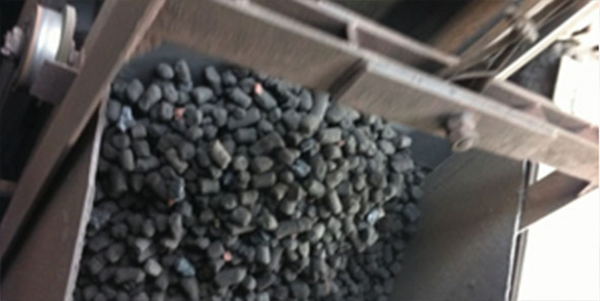
Strength of Cold Iron Ore and By-product Briquettes and Influencing Factors
Strength
The strength of cold iron ore and by-product briquettes is a prerequisite for their use in blast furnace smelting, and they typically require long curing times from production to furnace smelting. During this process, briquettes inevitably undergo collisions, impacts, and compressions, so they must have sufficient mechanical strength to ensure minimal or no fines generation during transportation, storage, and smelting, ensuring effective reduction in the furnace for smooth operation.
Additionally, due to plant management and curing conditions, these briquettes may be stored and cured outdoors. Due to environmental factors, the briquettes must have high cold strength in the early curing stage.
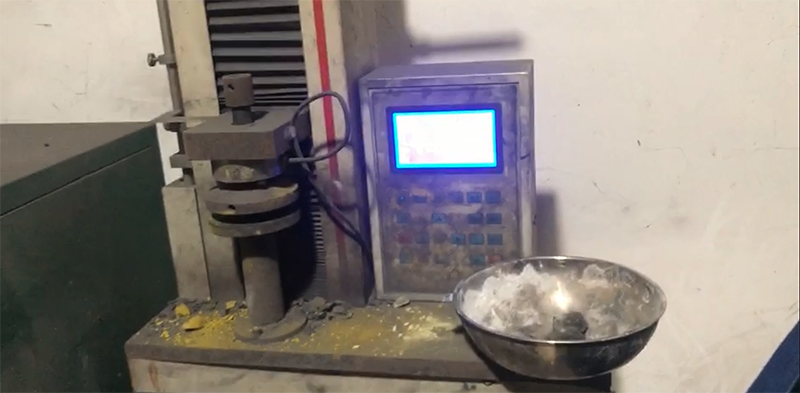
Raw Material Conditions Affecting Briquette Strength
The strength of cold iron ore and by-product briquettes largely depends on the chemical composition, mineral composition, and physical properties of the raw materials. Studies have shown that the strength of these briquettes increases as porosity decreases and particle size decreases, and the particle size distribution determines the density of the briquette and the number of contact points between materials. With an increase in fine materials in the mixture, the fine materials infiltrate the gaps between coarse particles, increasing the contact points between particles, enhancing density during briquetting, reducing the occurrence of coarse particle breakage under load, thereby improving cold strength.
Simultaneously, the addition of ultrafine powder strengthens solid-phase sintering, improving thermal strength. Briquettes made from large amounts of mill scale, BF dust, and coarse-grained return fines have more pores, fewer contact points, and poorer strength, resulting in substantial fines generation during transportation and storage. Therefore, a reasonable ratio of coarse to fine materials allows particles to fully rearrange and fill each other, enhancing mechanical interlocking force between particles and improving briquette strength.
Cold iron ore and by-product briquetting technology can use a wide range of iron-containing raw materials, including iron ore fines, return fines, and metallurgical by-products, which differ in their affinity for water. Besides hydrophilicity, the plasticity and brittleness of raw materials also affect briquette strength. If many brittle materials are incorporated, they may break under high molding pressure, reducing compressive strength. The surface characteristics and morphological features of raw materials also significantly affect briquette strength.
Binders
In the agglomeration process, binders play a role in wrapping and adsorbing material particles, enhancing the plasticity of the mixture. Additionally, binders penetrate the gaps between particles, increasing the contact area between particles. During curing, binders form bridges within the briquette, improving strength. Binders used in briquettes include inorganic binders, organic binders, and composite binders. Inorganic binders have good hydrophilicity and thermal stability, commonly used inorganic binders include cement, bentonite, sodium silicate, and lime; organic binders have better cold strength but poorer thermal stability, typically used in combination with inorganic binders.
Briquetting Processes
Briquetting processes mainly include roller briquetting, vacuum extrusion, and disc pelletizing.
Due to differences in agglomeration methods, the mechanical strength of briquettes varies. Roller briquetting and vacuum extrusion both use external pressure to mold the mixture through a die.
Roller briquetting produces briquettes by applying pressure with two rollers, but factors like roller speed and feed rate affect particle density, influencing briquette strength.
Vacuum extrusion removes over 90% of air through its vacuum chamber, significantly increasing density and uniformity, resulting in stronger briquettes compared to those produced by roller briquetting.
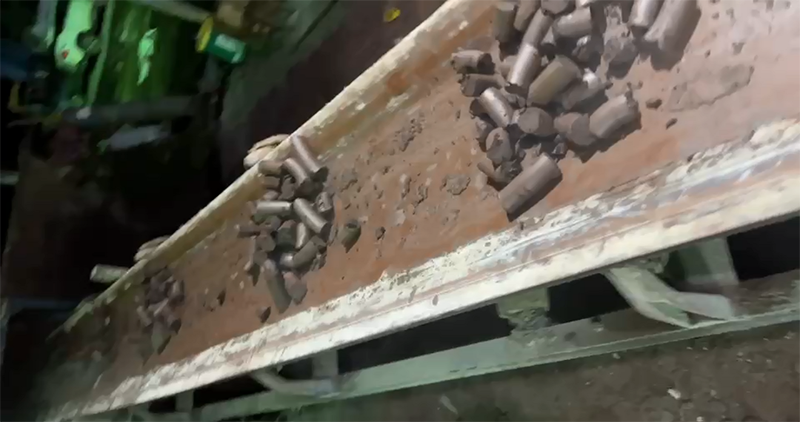
Economic Benefits of Using Cold Briquettes in Blast Furnaces
The technical and economic indicators of blast furnace ironmaking
Unique metallurgical properties allow cold iron ore and by-product briquettes to achieve remarkable results in blast furnace ironmaking.
Index of using cold briquettes in blast furnace from practice
Cold briquette ratio (w%) | Furnace volume (m3) | Coke ratio (kg/t)S | melted iron temperature (℃) |
0 | 2,800 | 502 | 1,517 |
0 | 45 | 686 | 1,380-1,440 |
5 | 2,800 | 490 | 1,523 |
80 | 45 | 530 | 1,440-1,450 |
100 | 45 | 490 | 1,440-1,450 |
Based on the table above, we can find that in different types of blast furnaces, as the proportion of these briquettes in the furnace charge increases, not only is the overall coke ratio reduced, but the temperature of the hot metal also rises, leading to an improvement in the effective volume utilization coefficient of the blast furnace.
Cost
The briquetting process has a wide range of raw material applicability and low requirements, allowing the use of iron ore fines, iron- and carbon-containing metallurgical by-products, return fines, etc. The lower cost of low-grade ores and metallurgical by-products translates to lower production costs for these briquettes. Compared to other forming processes, cold iron ore briquetting involves lower investment costs, no thermal treatment processes, shorter processes, and simpler technology.
For example, the vacuum extrusion process has simple equipment use and maintenance, with production costs of less than 10 USD per ton of briquette in China. In contrast, the cost of producing 1 ton of sinter is 120 USD in China. Additionally, the briquettes’ composition and metallurgical properties reduce coke and flux consumption in blast furnace ironmaking, further lowering overall costs.
Carbon Emissions
Cold briquetting technology effectively utilizes high TFe, high-carbon residues, low-grade ores, and return fines, forming a new composite briquette combining iron ore and carbonaceous materials. This low-carbon burden material aligns with the trend of developing low-carbon blast furnaces.
The primary carbon emission reduction impacts of using briquettes include:
- The cold briquetting and curing process reduces energy consumption associated with high-temperature roasting steps for furnace burden.
- Adding briquettes lowers the thermal reserve zone temperature, improving reduction efficiency and reducing furnace coke input by approximately 6% (based on comprehensive coke ratio, assuming carbon in briquettes displaces coke in a 1:1 ratio), achieving emission reduction.
- The presence of reducing agents reduces furnace coke input, lowering carbon emissions associated with coke production.
Considering these factors, using briquettes theoretically saves about 522 kg of CO2 emissions per ton of hot metal produced.