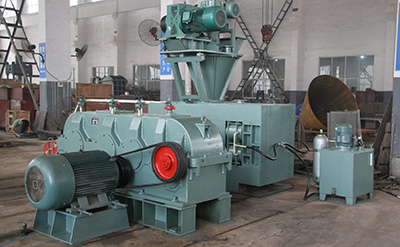
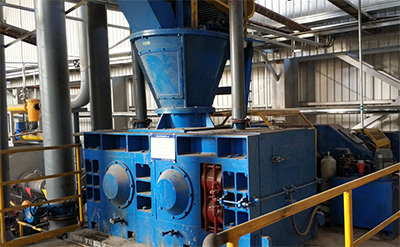
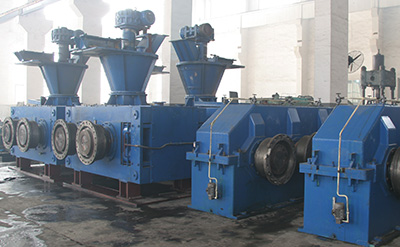
Cold roll briquette machine is a roll type briquetter used for room temperture briquetting work. It can work under a very high pressure and make briquette under a low moisture with shapes like oval, pillow, square, etc. Widely used in industries like metugally, mining, chemical, etc.
MAXTON supplies spare parts for roller briquette machines, including rollers, screws, and more, ensuring comprehensive support for your maintenance needs.
The material passes through the buffer bin, and then goes past the feeder, quantitatively and evenly enters the feed port of the roll briquette machine. After that, it reaches the pre-compression feeding device of the machine.
To maintain a stable material level in the pre-compression feeding device, the screw in the pre-compression feeding device will force the material into the middle of the rolls. The screw will pre-compress the material and remove the gas as much as possible from particles, and moves the material to be transported to the middle of two rolls.
At the arc-shaped notch of the rollers, the pockets of the same shape are evenly distributed on the surface of the two rolls. Through the meshing transmission of the synchronous gear reducer, the two rollers run at the same speed and opposite to each other, thus the material will be transported to the arc-shaped notch. The material is bitten into the groove and forced to compress. As the rolls continue to rotate, when they exceed the center line, the finished briquette will fall out of the pocket under the action of its own elasticity and gravity, thereby completing the process of briquette making.
1. Angle reducer 2. Main motor 3. Main gearbox 4. Coupling 5. Hydraulic station 6. Main frame 7. Screw feeding (optional)
Motor——V belt——Double shaft output reducer——Coupling——Rolls
Screw or double screw feeding or gravity feeding. Specially designed sealing structure.
Belt output or customized.
Surface is cold worked, beams are connected by high-strength bolts.
Central lubrication or point lubrication.
1. A layer of binder which is evenly wrapped on the surface of the material particles can greatly reduce the roughness of the particle surface, facilitates the sliding between materials;
2. When the material particles move relative to the pocket, the binder lubricates the ball socket, which greatly reduces the friction between the material and the ball socket, which is beneficial to briquetting and increases the service life of the roll.
Special binder can also help to improve the performance of the finished briquette like water proof, high high-temperature strength, etc.
Examples:
So many advantages of following a binder free briquetting way, raw materials are saved, a simple process, purer briquette, no harmful substances from binders, etc.
Binder-free briquette making, normally when the size of the raw material is suitable, the material is added to the briquetter at a constant speed and then make the briquette. In some cases, it is necessary to use the plasticity of the raw material under certain special conditions before briquetting.
Examples:
According to the characteristics, applications and pressure needed for different materials. Maxton’s cold roll briquette machines are divided into 3types: medium and low pressure roll press (specific pressing force ≤ 50kN/cm), high pressure roll press (specific pressing force ≥50kN/cm), extreme high pressure roll press (specific pressing force above 150 kN/cm).
Model | Roll diameter (mm) | Roll width (mm) | Total pressure (kN) | Specific pressing force (kN/cm) | Capacity (m3/h) | Main power (kW) |
ZY4320 | 430 | 200 | 1000 | 50 | 2.7 | 30-37 |
ZY4332 | 430 | 320 | 1000 | 30 | 4.5 | 30-37 |
ZY5235 | 520 | 350 | 1500 | 50 | 4.1 | 45-55 |
ZY5242 | 520 | 420 | 1500 | 30 | 7 | 45-55 |
ZY6540 | 650 | 400 | 2200 | 50 | 9.6 | 75-90 |
ZY6560 | 650 | 600 | 2200 | 30 | 14.4 | 75-90 |
ZY6548 | 750 | 480 | 3000 | 50 | 11.5 | 132-160 |
ZY7568 | 750 | 680 | 3000 | 30 | 16.6 | 132-160 |
ZY10090 | 1000 | 900 | 5000 | 50 | 27.5 | 2*(110-132) |
Optional:
Model | Roll diameter (mm) | Roll width (mm) | Total pressure (kN) | Specific pressing force (kN/cm) | Capacity (m3/h) | Main power (kW) |
GY430-100 | 430 | 100-120 | 1000 | 80-110 | 1.3-1.6 | 30-37 |
GY520-150 | 520 | 150-200 | 1500 | 80-110 | 2-2.7 | 55-75 |
GY650-220 | 650 | 200-270 | 2200 | 80-110 | 4.8-6.5 | 90-110 |
GY750-300 | 750 | 280 | 3000 | 110 | 6.7 | 185 |
GY800-380 | 800 | 350 | 3800 | 110 | 8.4 | 200 |
GY850-400 | 850 | 360 | 4000 | 110 | 9.5 | 250 |
GY1000-500 | 1000 | 500 | 5000 | 100 | 15 | 315 |
GY1200-800 | 1200 | 800 | 6000 | 125 | 23 | 500 |
GY1400-1000 | 1400 | 1000 | 10000 | 100 | 35 | 2*315 |
Optional:
Model | Roll diameter (mm) | Roll width (mm) | Total pressure (kN) | Specific pressing force (kN/cm) | Capacity (m3/h) | Main power (kW) |
CGY650-220 | 650 | 120 | 2200 | 200 | 2.9 | 132 |
CGY750-330 | 750 | 160 | 3300 | 200 | 3.8 | 200 |
CGY850-400 | 850 | 200 | 4000 | 200 | 5.3 | 250 |
CGY1000-500 | 1000 | 250 | 5000 | 200 | 7.5 | 315 |
CGY1200-800 | 1200 | 400 | 8000 | 200 | 11.5 | 500-560 |
Optional:
In briquetting, the binder is often the unsung hero. Whether you’re compacting…
Why Make Cold Iron Ore and By-product Briquettes With the shortage of…
What is water softnter salt briquette Water softener salt briquette, also known…
What is coke fine Coke fine refers to the small-sized particles or…
Why Deoxidation in Steelmaking Deoxidation plays a dual role in the steelmaking…
What is red mud Around 1888, Austrian chemist Carl Josef Bayer developed…