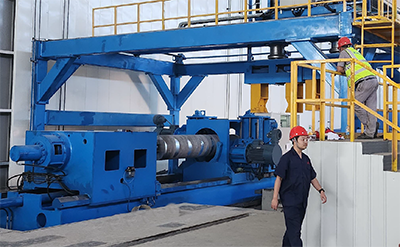
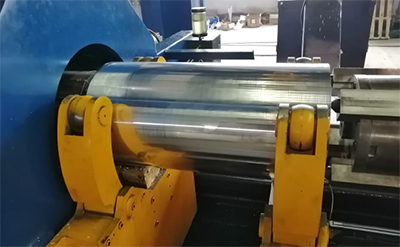
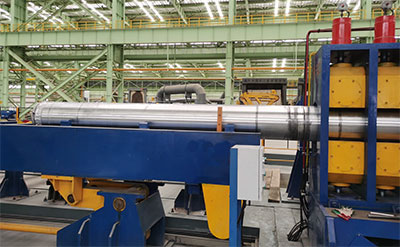
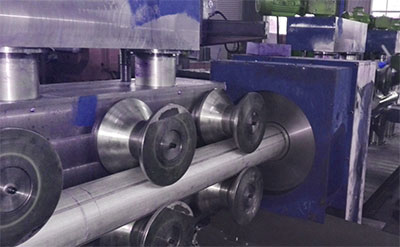
With the development of modern manufacturing, metal bars have been widely used in the industrial field. To ensure product quality, industries generally use peeling machines for surface treatment of bars, obtaining bars that meet the required dimensions and precision.
Metal turning peeling is a highly efficient surface processing technology that can quickly remove decarburized layers, cracks, and other defects from the surface of bars, achieving high-precision bright material standards. It is an effective method for improving metal surface quality, especially advantageous for processing long bars. Continuous turning of the entire bar significantly increases efficiency, making it several to dozens of times more efficient than conventional processes.
The bar peeling machine completes loading through a feeding rack. The bar is conveyed into the main working area via rollers and the clamping rollers of the feeding carriage. While the bar is clamped, it is slowly fed forward. The machine’s cutter head is fixed on a large-diameter hollow shaft, which is driven by the main motor through a reducer, causing both the hollow shaft and the cutter head to rotate at high speed. This enables high-speed cutting of the bar passing through the center.
The cutter head is equipped with tool holders, each containing carbide inserts. During a single turning process, the carbide inserts perform multi-layer peeling of the bar, achieving a certain surface roughness. Behind the cutter head, a set of polishing rollers further processes the peeled bar surface.
At the machine’s exit, a laser measurement device dynamically measures the diameter of the peeled bar and feeds the results back to the computer-controlled main unit, which adjusts the cutting depth accordingly. The bar’s feeding process is primarily completed by the front feeding carriage and the rear pulling carriage. Their switching and the entire turning process are fully automated under the control of the main unit’s program.
All parameters of the peeling machine, such as feed rate and rotation speed, can be adjusted via the control interface on the operation panel.