Granulation, Why?
Potassium chloride granular has a higher nutrient utilization rate in the soil compared to powdered potassium chloride. This is because granular fertilizers reduce deep leaching, loss, volatilization, fixation as insoluble compounds, and have a prolonged fertilization effect. Additionally, granular potassium chloride has good storage, transportation, and application performance, with outstanding flowability, making it easier to spread during fertilization. It also does not easily clump after long-term storage. According to the different nutrient requirements of various soils, crops, and fertilization periods, other fertilizers of similar particle size can be added to provide excellent conditions for overall nutrient utilization. This can also reduce the slow-release rate of fertilizers, promote the good absorption of crops, and improve fertilizer utilization efficiency.
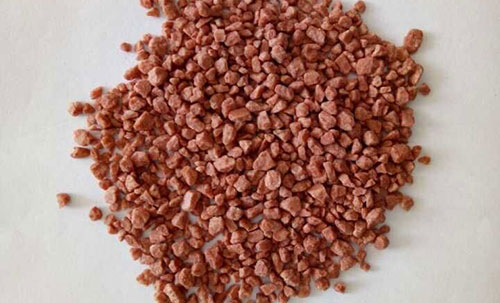
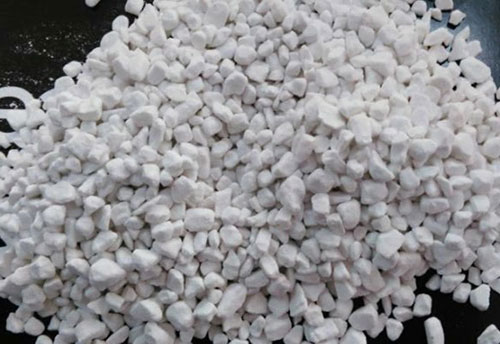
Compaction of KCl
The typical method for secondary processing granulation of powdered potassium chloride is roller compaction.
Theory of Roller Compaction
The principle of roller compaction mainly involves the agglomeration of dry material into dense and hard flakes or ribbons under pressure, known as the compaction process. The function of compaction is firstly to expel the air between particles, and secondly, to bring the particles close enough to generate Van der Waals forces, adsorption forces, crystal bridges, and embedded connections. The strength of the granules formed through roller compaction mainly relies on the intermolecular forces. This process is simple, entirely physical, relatively low in investment, only requires electricity as an energy source, has low processing costs, and is particularly suitable for heat-sensitive materials.
Features
- Low Energy Consumption: Production only requires electricity and a small amount of cooling water (depending on the raw material condition), with about 35 kW·h of electricity consumed per ton of product.
- Binder free: Dry granulation does not require additional additives, utilizing the intermolecular forces of the material itself, simplifying the process, reducing consumption, and having no impact on product quality.
- Low Investment: Due to the elimination of the drying process, the process flow is simple, and the investment is low.
The System
The system includes three parts:
- Storage, dosing, and mixing;
- Compaction;
- Crushing and screening.
The main equipment includes a roller compactor, crusher, and screener, as well as other material storage and handling equipment.
Potassium fertilizer produced by compaction granulation has sufficient strength, low dust, no caking, narrow particle size distribution, good flowability, and the only drawback is that the product particles are irregular in shape (can be polished for better shape), but this does not affect using these granules.
Compaction/granulation is now an important stage in the overall potassium chloride production/beneficiation process. Compaction implies the agglomeration of particles under force to produce a densified and coherent sheet-like material referred to as flake. In this case, granulation refers to the dry milling of flake into a prescribed size distribution employing a screening step. Rounding off / polishing of the broken material can be performed in an additional drum. Compaction/granulation of potash began in the 1950s. Currently, about 60% of the total world potash production for fertilisers application is compacted.