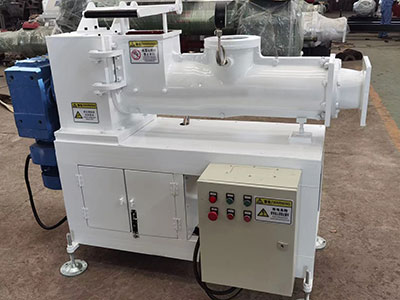
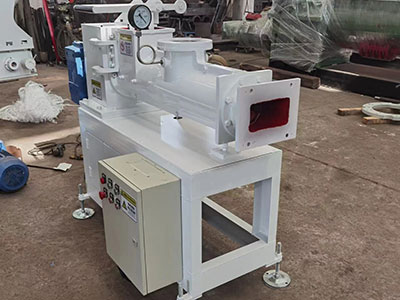
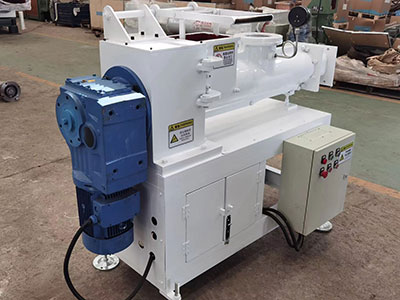
A new bench-scale laboratory and pilot type vacuum extrusion machine has been developed by Maxton, designed specifically for research and small laboratory projects. Model JC150, small extruder can provide conclusive extrusion tests on a variety of materials with samples as small as 20-50kgs.
The die is easily removable for quick setup changes, cleaning and sterilization. An integrated mixing system accommodates preparation of small batches with binders or other additives, then deposits the mixed material directly into a feeding hopper.
It also can be a dedicated pilot extrusion machine that’s also capable of continuous small-batch production provides a lower cost alternative whilst delivering excellent results compare to full scale machines. It has been designed to offer the flexibility of a small device for product design and evaluation together with the capacity to operate as a small batch production briqueter.
It also can be used to train staff to run a production plant.
The JC150 lets you see the results of changing your variables immediately. You can calibrate with precision to optimize your product performance:
Extruded shapes exit the die ready for product analysis. You can measure drying, firing and curing cycles, compressive strength and density, and conduct drop testing or trembling tests.
This extruder replicates production at a smaller, more affordable scale. The result is rapid prototyping and accelerated product development — for ROI measured in weeks or months, instead of years.
In briquetting, the binder is often the unsung hero. Whether you’re compacting…
Why Make Cold Iron Ore and By-product Briquettes With the shortage of…
What is water softnter salt briquette Water softener salt briquette, also known…
What is coke fine Coke fine refers to the small-sized particles or…
Why Deoxidation in Steelmaking Deoxidation plays a dual role in the steelmaking…
What is red mud Around 1888, Austrian chemist Carl Josef Bayer developed…