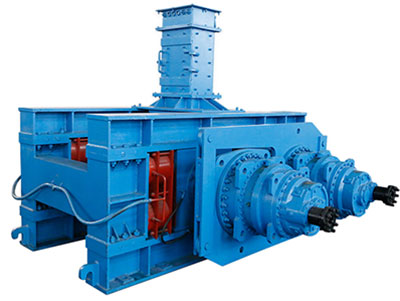
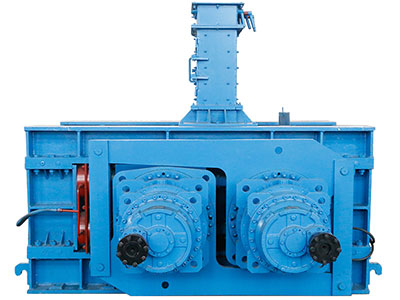
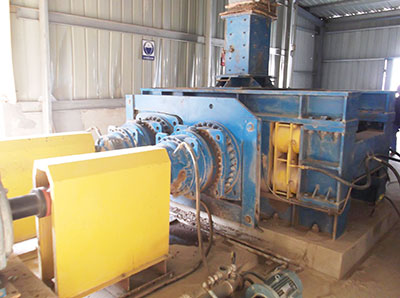
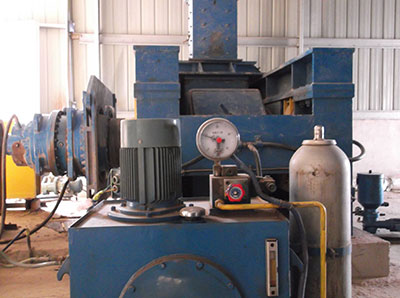
Long-term work practice shows that the energy consumption and wear part consumption of the crushing process are significantly lower than those of the grinding process, so more crushing and less grinding is an important principle that should be adhered to in the material crushing process. High pressure grinding rolls or HPGR is such a kind of equipment that uses this principle for crushing operations.
HPGR has been widely used in fine crushing of metal ore beneficiation plants, crushing in cement industry, granulation in chemical industry and fine grinding of pellets to increase specific surface area. It can replace the fine crushing operation, realize more crushing and less grinding, improve system production capacity, save energy and reduce consumption, and have high reliability.
The material is fed by the feeding device between two rollers rotating in opposite directions, and the rollers exert a large extrusion pressure on the material.
The first is that the irregularly shaped large material blocks are subjected to point contact pressure, which reduces the overall volume of the material and tends to be dense, and moves down with the rollers. At the same time, the material is also changed from point contact pressure to line contact pressure, making the material more dense. With the sharp increase of material density, the internal stress also rises rapidly. When the material passes through the minimum gap between the two rollers, it will be subjected to greater pressure, making the internal stress of the material exceed its compressive strength limit. At this time, cracks begin to appear inside the material and continue to expand, causing the material to break from the inside. , forming small cake-like pieces that shatter when moved. In the next process, it is broken down using only a small amount of energy.
Due to the relatively weak force at the joints between different minerals in the ore, cracks are more likely to occur in these parts during the crushing process of the high-pressure roller mill. The degree of monomer dissociation was significantly higher.
1. Fixed roll 2. Feeding chute 3. Floating roll 4. Lubrication oil station 5. Motor 6. Reducer 7. Coupling 8. Hydraulic station
Roll can be the type of built-up welding, compound or inlay.
Built-Up Welding | Compound | Inlay | |
Material | Cement raw meal, cement clinker, etc. Material with low hardness | Cement raw meal, cement clinker, etc. Ores with relatively high hardness | Ores with higher hardness |
Roll cost | relatively low | relatively high | high |
Service life (h) | 8,000 | 30,000/10,000 | 20,000 |
Running cost | relatively low | medium | low |
Texture | ![]() | ![]() | ![]() |
Through hydraulic coupling, the universal connector is connected with the motor. Smooth start, and the reducer adopts planetary gear transmission.
Open lubrication.
IRON ORE
HPGR and ball mill are both widely used ore crushing (grinding) equipment.…
High-pressure grind roll are widely used in major mines and related material…
Situation on Non-Ferrous Metal Ore Grinding In the actual production of various…