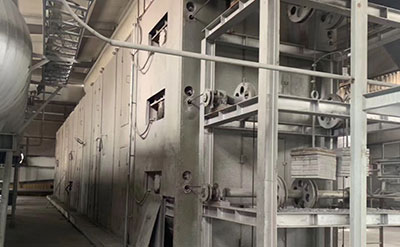
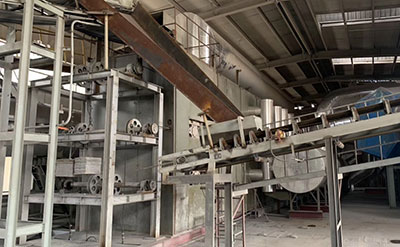

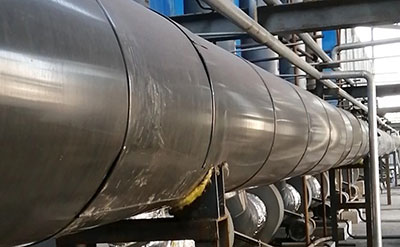
Belt dryer, also referred to as a belt cooler, with convection drying technology derived from tunnel drying, belongs to the category of continuous static dryers. In this method, the material to be dried is placed on a conveyor belt inside a drying tunnel, where it undergoes mass and heat transfer with the heat source inside the tunnel, thus achieving the drying process. The entire belt drying process system parameters can be set in a stepwise combination, ensuring the superiority, reliability, and flexibility of the drying process.
It is an equipment designed for the particularly gentle thermal treatment of product.
The product is distributed on an endless, air permeable conveyer belt and is flooded with heated air. The drying air is circulated and saturated with each pass though the product layer. A specific part of the drying air is replenished with fresh air and at the same time corresponding vapours are removed. For optimum energy efficiency the drying air is directed against the product flow.
In case a uniform treatment over the entire product layer height required, the air direction changes at least once from upstream to downstream. Often a cooling section follows. Here, the cold air passes from top to bottom through the product. The heated exhaust air can be used for the drying section. In case of very slow running processes, our belt dryers can be designed as multi-belt systems.
Optimal material handling and output
Depending on the requirements, the appropriate technology is selected in consultation with the customer.
The product is typically placed on the dryer belt via swivel chutes, swivel belts, product chutes, vibration chutes and similar systems.
After the drying process, the product leaves the dryer via vibrating chutes, slides, discharge conveyors or screws.
We offer a variety of techniques for material infeed and discharge, which we select in consultation with you according to your requirements. The product is typically fed in via swing conveyors, swing belts, product conveyors, vibratory conveyors and similar systems. After the drying process, the product leaves the dryer via vibrating conveyors, slides, discharge conveyors or screws.
Depending on the local conditions, thermal oil, saturated steam, waste heat from combined heat and power and ORC processes or already heated process air can be used flexibly as heating media.
Heat generators
– Gas, oil, biomass or electric boilers
– Gas burners, direct or indirect
Heat carriers
– Hot water, steam or thermal oil