Why Granulation?
The purposes vary according to the applied industry, but generally include the following aspects:
- For accurate quantification, dosing, and management, such as producing various types of drug tablets.
- To prevent dust dispersion and adhesion to vessel walls; serious dust dispersion and adhesion of powders can be prevented after granulation, reducing environmental pollution and raw material loss, such as in the production of granular pesticides.
- To prevent segregation of various components; when there are differences in particle size and density among components in a formulation, segregation is prone to occur, which can be effectively prevented by granulation before or after mixing.
- To prevent agglomeration during the production of certain solid-phase materials; for example, in the production of granular phosphorus and urea, granules generally have larger particle size than powders, and the specific surface area of materials after granulation is greatly reduced. The number of particles that can be contacted around each particle is reduced, thus reducing adhesion and aggregation significantly, improving flowability of granules. For instance, spray granulation of ceramic raw materials can significantly enhance the stability during molding feed.
- To reduce the hazards in handling toxic and corrosive materials during processing operations; such as compressing caustic soda into sheets or granules for use.
- To adjust bulk density and improve solubility performance; for example, in some instant food products.
- To adjust the porosity and specific surface area of the final product; such as in the production of catalyst carriers and porous refractory insulation materials.
- To improve heat transfer efficiency and aid combustion; such as in the firing process of rotary kiln cement.
- For ease of use, convenient transportation, and to enhance commercial value, etc. Granular formulations are made by granulation methods according to corresponding formulations.
Maxton’s Granulators
Fields of Applications
- Chemicals powders (sodium carbonate, sodium chloride, sodium sulphate, sodium nitrate, sodium humate, ammonium chloride, iron sulphate, calcium chloride, calcium nitrate, calcium sulfate, deicing salt, lithium carbonate, aluminum Fluoride, foundry additives, foundry salts etc…)
- Fertilizers (PK, NPK, potassium chloride, potassium sulphate, ammonium sulphate, potassium nitrate, phosphate, potash slag, micronutrients, urea…)
- Detergents
- Industrial disinfectant (trichloroisocyanuric acid)
- Antioxidant
- Animal antibiotics
- Polymers, xantathe
- Coal or charcoal for production of activated carbon
- Oxides (uranium oxide, uranium hexafluoride, chromium oxide, iron oxide, zinc oxide, …)
- Minerals (burnt lime, dolomite, magnesia, …), ores
- Paint pigments
- Thermoplastic additives
- Nickel ore dust
- Clay, bentonite
- Dried sewage sludge, vibrating sludges
- Catalysts
- Kaolin
- Graphite
- Limestone / Gypsum
- Cement / Lime Kiln Dust
- Flyash
- Filter / Centrifuge Cake
- Pond tailings
- Dust from steel plant, EAF dust, BF dust, etc.
Feasibility study
- Laboratory machines enables our client to conduct the granulation feasibility studies on a wide variety of products in very small quantities (about 10-20 kg for one test)
- The studies include the performance on granulation and strength tests
- If the results of the tests meet the client’s requirements, the project can move forward
MAXTON’s granulation services:
1. Basic and detail engineering of compaction and granulation units
The engineering department is in charge of drawing-up the preliminary project drawings and then ensures the basic and detail engineering of the briquetting and compaction-granulation units. This department provides customers with important services ensuring the integration of equipment into the process in each application and ensuring that the material meets the required specifications.
2. Design and manufacture of the equipment of compaction and granulation units
Equipped with CAD Softwares, the engineering department and its skilled technicians and engineers realize the design of the key-equipment (crusher, dryer, mixer, press, granulator, polishing-coating drums, screen, packing, handling and storage equipment) integrated in the briquetting and compaction-granulation units.
3. Technical assistance for mounting and commissioning
MAXTON has a group of skilled personnel who can go to the site to assist in the commissioning and maintenance. We understand that downtime could be costly, and our field technical staff is well-qualified to ensure the smooth operation of your business as soon as possible.
4. Training of operators
After the erection and the commissioning completed, MAXTON ensures the training of the operators by instructing them about all they need to know about operation, lubricating, safety and mechanical/electrical maintenance purposes on our equipment. Our instructors have rich and long experience regarding the equipment life and give precious advises to the operators so that they are able to ensure by themselves the continuous running of the equipment.
5. Supply of spare parts
Although the MAXTON equipment are heavy-duty designed to operate in difficult conditions with continuous running, it is therefore necessary to replace wearing parts or to get safety spare-parts at customer warehouse disposal in order to be able to maintain the equipment in place very quickly and reduce the production downtime. MAXTON ensures the supply of spare parts, without time limit for the parts manufactured by itself. MAXTON is also able to supply spare-parts for equipment delivered by others.
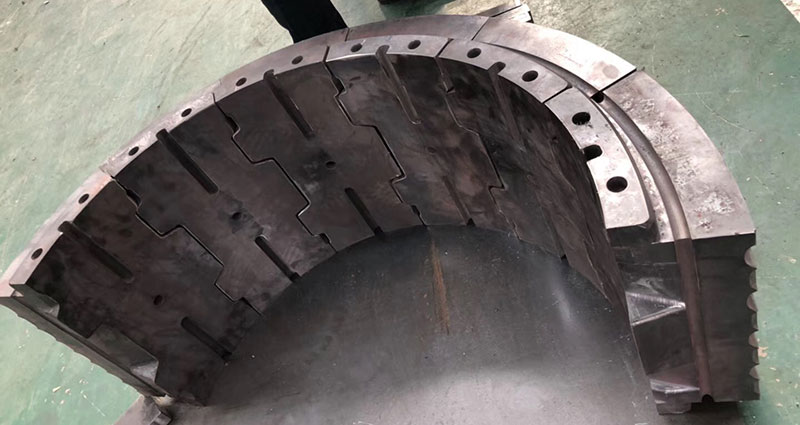