What is an oil pumping unit
An oil pumping unit, also known as a pump jack, nodding donkey, horsehead pump, rocking horse, or grasshopper pump, is a mechanical device used in the petroleum industry to extract crude oil from underground reservoirs. These units are commonly seen in onshore oil fields and are iconic symbols of oil production.
Main energy consumption for a pumping unit
The energy consumption of the pumping unit mainly includes mechanical energy loss, oil kinetic energy loss and thermal energy loss.
The main sources of mechanical energy loss include the mechanical loss of the oil pump transmission system and the mechanical loss of accessories. The mechanical loss of the oil pump transmission system is mainly caused by the rolling friction of the bearings, the meshing friction between the gears, and the friction between the shaft and the sleeve. Mechanical losses of accessories include energy consumption of oil pump accessories such as shaft seals, sealing devices, cooling devices, etc.
Oil kinetic energy loss mainly includes pipeline friction loss and local resistance loss. Pipe friction loss refers to the energy loss caused by the friction between the oil and the pipe wall when the oil flows. Local resistance loss refers to the energy consumption caused by local devices such as throttling, elbows, and elbows in the pipeline system.
Thermal energy loss mainly includes friction heat energy loss and leakage heat energy loss. Frictional heat energy loss refers to the energy loss caused by the relative sliding between gears, bearings and other components in the oil pump transmission system. Leakage heat energy loss refers to the energy consumption caused by oil seal failure or leakage during the operation of the oil pump.
There are some other energy consumption that need to be considered, such as electrical energy loss, cooling energy consumption, etc. Electrical energy loss refers to the energy consumed by oil pump driving equipment (such as motors) during work. Cooling energy consumption refers to the energy required to cool the oil pump or accessories during operation.
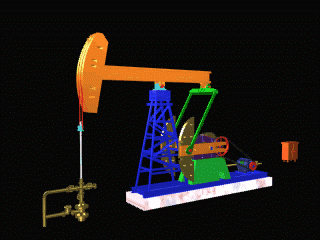
Analysis of total energy consumption by each energy consumption component
Before analyzing the energy consumption components of the pumping unit, it is first necessary to clarify that the total energy consumption of the pumping unit is composed of mechanical energy loss, hydraulic energy loss, thermal energy loss and other energy consumption (like electrical energy loss, cooling energy consumption, etc. ) are composed together.
Among them, the proportion of mechanical energy loss = (bearing friction loss + gear meshing friction loss + shaft and sleeve friction loss + accessory mechanical loss) / total energy consumption;
Proportion of hydraulic kinetic energy loss = (pipeline friction loss + local resistance loss) / total energy consumption;
Thermal energy loss proportion = (friction heat energy loss + leakage heat energy loss) / total energy consumption.
In addition to the above three major energy consumption components, we also need to consider the contribution of electrical energy loss and cooling energy consumption to the total energy consumption.
Among them, the proportion of electrical energy loss = energy consumption of oil pump driving equipment/total energy consumption;
Cooling energy consumption ratio = energy consumption of cooling oil pump or accessories/total energy consumption.
According to actual operating data statistics, the energy consumption proportions are shown in the Table below.
Consumption type | Percentage of total energy consumption |
Mechanical energy loss | 60 |
Oil kinetic energy loss | 25 |
Thermal energy loss | 5 |
Electrical energy loss | 5 |
Cooling energy consumption | 5 |
- Mechanical energy loss: accounts for 60% of the total energy consumption. This is the energy loss caused by friction and wear of mechanical equipment during the operation of the pumping unit.
- Hydraulic kinetic energy loss: accounts for 25% of the total energy consumption. This part of the energy loss mainly occurs during the pumping process of the oil pumping unit, and is caused by the resistance generated when the liquid is transported in the pipeline.
- Thermal energy loss: accounting for 5% of the total energy consumption. During the operation of the pumping unit, energy loss occurs due to the heat generated by the oil pump, motor and other equipment.
- Electrical energy loss: accounting for 5% of total energy consumption. This part of the energy loss mainly occurs in the electrical equipment part of the pumping unit, including the loss of transformers, cables and other equipment.
- Cooling energy consumption: accounts for 5% of the total energy consumption. Cooling energy consumption is the energy required by the cooling system to ensure the normal operation of the pumping unit.
Based on the above analysis, the following conclusions can be drawn:
- The energy consumption of the pumping unit is mainly concentrated in mechanical energy loss, hydraulic kinetic energy loss and thermal energy loss, of which mechanical energy loss accounts for the highest proportion, followed by hydraulic kinetic energy loss, and thermal energy loss is the lowest;
- Electric energy loss Loss and cooling energy consumption account for a relatively low proportion of total energy consumption, but still require attention and optimization to reduce energy consumption of the entire system.
Technical measures and principles for energy saving and consumption reduction of oil pumping units
Power system
High efficiency motor
The core principle of high-efficiency motors is to reduce current losses and mechanical conversion losses. In the design of the motor, an efficient electromagnetic design and a copper rotor are used to reduce resistance and copper losses. In addition, the use of advanced magnetic materials and optimized magnetic circuit design can greatly improve the magnetic circuit conduction performance of the motor and reduce magnetic field losses. The manufacturing process of the motor also has a direct impact on its energy efficiency. The use of precise processing technology and high-quality materials can effectively reduce friction loss and mechanical noise and improve the operating efficiency of the motor. In addition to the design and manufacturing of the motor itself, the application of high-efficiency motors also requires other energy-saving technical means. For example, in the control system of the oil pumping unit, advanced frequency conversion speed regulation technology and efficient induction motor control algorithm are applied to achieve optimal operation of the motor and electric energy regulation. In addition, combined with intelligent monitoring and diagnostic technology, the operating status and load changes of the motor can be monitored and analyzed in real time, and operating parameters can be adjusted in a timely manner to achieve efficient energy consumption management.
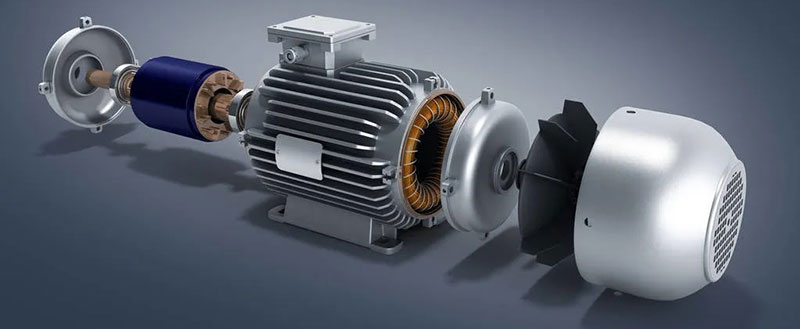
VFD
In response to changes in the load of the pumping unit, VFD technology can automatically adjust the motor so that it always works at the optimal efficiency point. During the operation of the pumping unit, the load will fluctuate with changes in oil well production. VFD technology can automatically adjust the motor speed according to the load to avoid overload or underload operation of the motor, thereby improving energy utilization. VFD technology can realize soft start of pumping units, reduce starting current and reduce the impact on the power grid. During the startup process of the pumping unit, the use of VFD technology can avoid the large current impact generated when the traditional motor is started, reduce the impact on the power grid, and improve system stability. By adjusting the motor speed of the pumping unit in real time, VFD technology can effectively reduce the energy consumption of the pumping unit. During the operation of the pumping unit, according to the oil well output and the working status of the pump, VFD technology can automatically adjust the motor speed to match the pump displacement with the oil well demand and avoid energy waste. VFD technology can also be combined with intelligent monitoring systems to achieve remote monitoring and fault diagnosis of pumping units. By monitoring the operating parameters of the pumping unit in real time, the intelligent monitoring system can analyze the operating status of the pumping unit, handle abnormal situations in a timely manner, and ensure the stable operation of the pumping unit.
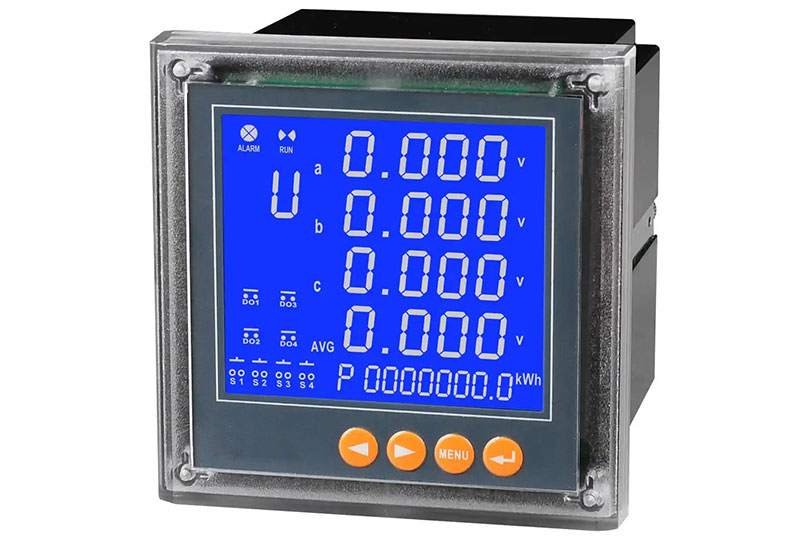
Structural design
Material selection and optimized design
In the work of beam pumping units, key components such as beams and cranks can be made of materials with high strength and wear resistance to ensure long-term stable operation. You can also choose high-efficiency, low-energy-consumption motors and frequency converters to reduce the overall energy consumption of the system.
In terms of optimized design, professional knowledge and skills should be used to conduct in-depth research on the structure, performance, and working principles of the pumping unit to improve equipment operating efficiency. For example, mechatronics technology and electronic information engineering technology can be used to intelligently control and monitor the pumping unit to achieve remote diagnosis and automatic adjustment, thereby reducing energy consumption. At the same time, explore the use of new transmission methods, such as planetary gear transmission, hydraulic transmission, etc., to improve transmission efficiency and reduce energy loss.
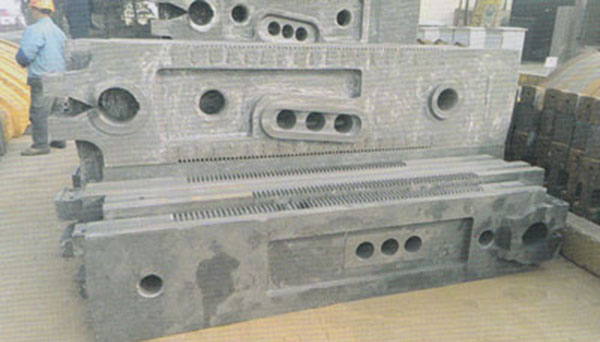
Improvements in lubrication and sealing technology
High-efficiency lubricants, such as high-temperature lubrication brittle solid lubricants, can be used to reduce the amount of lubricant used and improve the lubrication effect. The lubricant has a low friction coefficient and good high temperature resistance, and can reduce energy loss caused by friction.
In addition, the use of penetrating lubricating grease, such as polytetrafluoroethylene (PTFE) lubricating grease, can improve the quality of the oil film and reduce friction, thereby reducing energy consumption. In terms of sealing technology, efficient sealing materials such as polytetrafluoroethylene (PTFE) and fluororubber seals can be used to reduce leakage and damping losses. PTFE has excellent chemical resistance and high temperature resistance, and can effectively block oil and gas leakage and reduce energy loss. Fluorine rubber seals have good elastic recovery and oil resistance, can maintain good sealing effect and reduce energy loss. Strengthen the precision control of sealing parts, including the flatness and dimensional accuracy of the sealing surface, to ensure the maximum sealing effect.
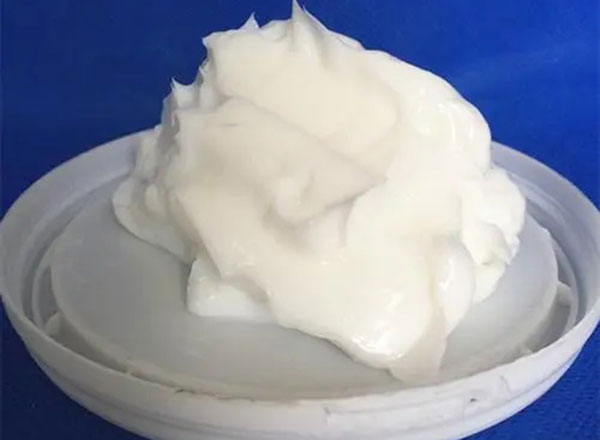
In addition, there is a need to improve the design of the pumping unit’s lubrication and sealing systems. The lubrication system can adopt a circulating lubrication system to enhance the supply and recovery of lubricating oil and reduce waste and energy consumption.
At the same time, an active control system is used to dynamically adjust the lubricating oil film to adapt to the needs of different working conditions and further improve lubrication efficiency and energy saving effects. In terms of sealing systems, high-precision sealing design and enhanced maintenance of sealing components can be introduced to ensure long-lasting and stable sealing performance and reduce energy loss.
Technical means to reduce friction and wear
Through surface modification techniques, such as coating and plating, the hardness and wear resistance of the surface of components subject to friction can be improved.
For example, using coating technologies such as physical vapor deposition (PVD) and chemical vapor deposition (CVD), coatings with high hardness and low friction coefficient, such as molybdenum disulfide (MoS2) and diamond films, can be formed on the friction surface.
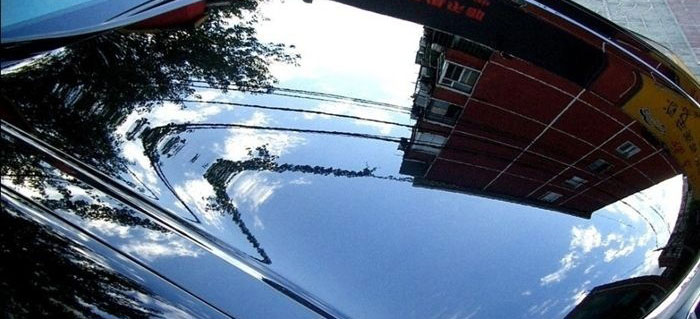
These coatings reduce direct contact between contact surfaces, reducing wear and friction. Conventional lubricating greases can also be used, and these can have their lubrication properties improved by adding friction and anti-wear agents. For example, adding solid lubricating additives such as graphite or molybdenum disulfide can form a lubricating film to reduce the contact between metal surfaces and reduce wear.
In addition, the use of lubricating oil viscosity control technology, such as multi-grade viscosity oil and lubricating oil with reduced viscosity index, can provide better lubrication performance and reduce friction and wear under high temperature and high-speed working conditions.
Tribology and wear theory can also be used to reduce friction and wear by designing and optimizing the mechanical structure and process parameters of the pumping unit. Friction loss and wear can be reduced by reducing contact pressure, reducing relative motion speed and reducing local vibration.
Considering the parts themselves, precision manufacturing technology and high-precision processing technology can be used to improve the smoothness and precision of the component surface and reduce the occurrence of friction and wear.
Management
In terms of operation management and energy-saving technology, the key to optimizing operation and adjusting processes is to improve the energy utilization efficiency of equipment, reduce energy consumption, and reduce energy waste.
- Advanced automatic control systems can be used to realize automated operation and management of pumping units. By collecting and analyzing the operating data of the pumping unit, the working status of the equipment can be monitored and adjusted in real time to improve the operating efficiency of the equipment.
- Advanced instrument and sensor technology is used to realize online monitoring and automatic control of the pumping unit, which can detect and deal with abnormal conditions of the equipment in a timely manner and effectively avoid the waste of energy.
- The process of the pumping unit can be optimized and adjusted to reduce energy consumption. By analyzing the energy loss points in the production process, we can take corresponding technical measures to improve them.
Conclusion
Through the energy consumption analysis of the pumping unit, energy-saving technical measures in three aspects: power system, structural system and operation management are discussed in detail. These technologies can play a positive role in reducing energy consumption of pumping units. However, there are still some unresolved issues and technical challenges that need to be improved. Therefore, we should further explore the application effects of energy-saving and consumption-reducing technologies, continue to improve and innovate technical means, and combine them with existing oil field mining processes to achieve more efficient and environmentally friendly oil field mining. This will make a positive contribution to the sustainable development of the oil industry.