Why drying coal sludge
Coal sludge generally refers to a semi-solid substance formed by coal powder with water. It is a by-product of the coal washing and processing process, with a particle size of less than 0.5 mm. There are many types of coal sludge, and its uses are wide-ranging. Depending on the type and formation mechanism, its properties can vary greatly, and so can its usability. Because coal sludge has strong water retention and high moisture content (usually above 30%), and because it generally contains a lot of clay minerals with low calorific value and fine particle composition, most coal sludge is highly sticky, making it difficult to apply industrially. Thermal power plants can significantly save economic costs by co-firing coal sludge, but due to its high moisture content, the proportion of sludge in the mix should be relatively small.
If there are no effective means and methods to dispose of coal sludge, not only is the resource wasted, but it also causes serious environmental pollution. If coal sludge is not reasonably utilized and is stored for a long time, it will occupy a lot of land, and in a piled state, it is extremely unstable, losing shape in water and blowing away when dry. Sometimes, it even restricts the normal operation of coal washing activities. Using a rotary dryer to dry coal sludge can further increase its added value. After drying, coal sludge can significantly reduce total moisture content, further increase its calorific value, and after treatment, the coal sludge can be mixed with middlings for transportation and sales, avoiding issues in cold regions where mixed coal sludge and middlings may freeze in transit, affecting the quality of the middlings.
In general, the production of coal sludge in mining areas is continuous. For the same type of coal, the coal sludge produced after washing and filtering has good consistency in physical and chemical properties. A typical production and physical and chemical characteristics from the ore dressing process are shown in the table below.
Coal sludge treated by a plate filter press has high moisture and strong stickiness. Its calorific value is generally between 8.50 and 12.50 MJ/kg, which can meet the requirements for blending and burning for power coal, but the drying problem needs to be solved to ensure smooth blending and utilization of its combustion value.
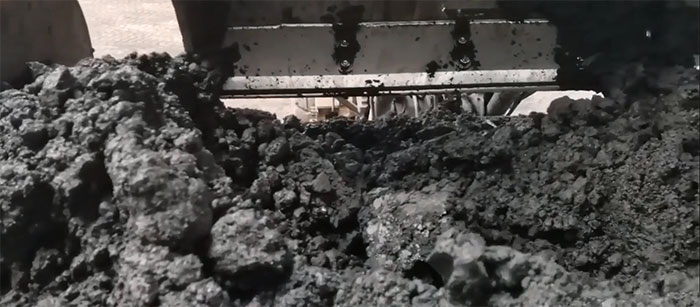
Structure of the Coal Sludge Drying System
The rotary dryer, known for its safe and reliable operation, simple operation, and high thermal efficiency, is the main equipment for drying coal sludge.
The rotary drying equipment for coal sludge mainly consists of dispersing device, conveying device, heat source device, feeding device, drying device, discharging device, draft and dust removal device, and other structural components.
After being filtered by the filter press, the coal sludge is sent into the dryer for drying.
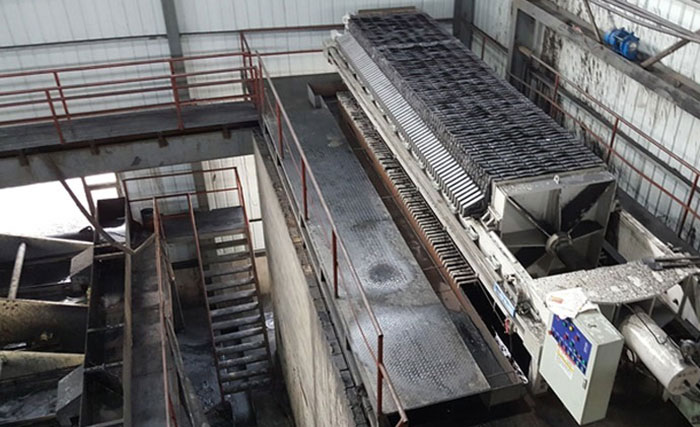
Drying Principle of the Equipment
The main working principle of rotary drying equipment is to use high-temperature flue gas generated by the combustion device, which is the heat source, to heat the high-moisture coal sludge in a concurrent flow manner. The coal sludge undergoes a series of physical and chemical state changes inside the equipment, gradually reducing its moisture content through heat exchange with the high-temperature airflow in different stages inside the drum, forming a usable fuel coal for direct blending and combustion.
Drying Process: The filter cake of coal sludge processed by the filter press is conveyed to the rotary dryer by a coal sludge conveyor belt. To ensure uniform and controllable feeding, a controllable coal sludge scraper conveyor is installed at the inlet. At the same time, a blower draws air into the hot blast stove, heats it, and then sends it to the rotary dryer. The heated high-temperature hot air flows through the coal sludge, undergoing repeated tearing, lifting, scattering, and crushing processes, fully contacting and absorbing the moisture, which is then extracted by the induced draft fan, achieving the drying effect. The dried material is finally output through a belt conveyor.
The drying process mainly involves the coal sludge material passing through the dispersing zone, guide zone, cleaning zone, lifting board zone, and discharging zone sequentially after entering the rotary drying equipment, ultimately achieving drying. In the dispersing zone, the wet coal sludge is fed into the dispersing device by the conveying system. After quick dispersing, it forms blocky coal sludge, which is then sent into the dryer under negative pressure. In the guide zone, the coal sludge rapidly evaporates a large amount of water upon contact with the high-temperature negative pressure hot air. Under the action of the large-angle lifting board, the coal sludge is sent to the cleaning zone before agglomeration. In the cleaning zone, the cleaning device can quickly and effectively clean off the coal sludge sticking to the drum wall, and it also has a good crushing effect on the agglomerated material, further increasing the heat exchange area and improving the efficiency of heat and mass transfer. In the lifting board zone, the drying temperature is relatively low, the coal sludge is in a low moisture, loose state, with no significant agglomeration phenomenon. After heat exchange, it reaches the required moisture content for the finished product. In this zone, the coal sludge rolls and slides to the discharge port without lifting boards, and the dried coal sludge is transferred to the storage yard by the conveying device, completing the entire drying process.
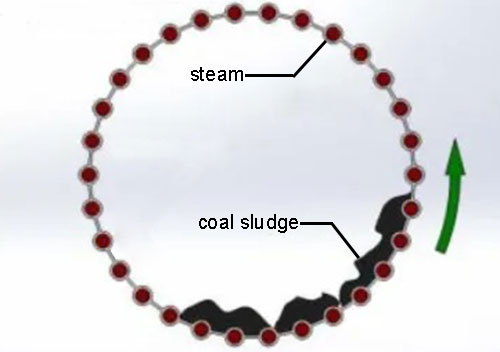
Features of the Drying Equipment
The coal sludge rotary dryer uses concurrent airflow for heating, with the drying flue gas and wet coal sludge entering the equipment from the same side, fully utilizing the high-temperature flue gas to achieve a strong evaporation intensity. At the material outlet, the lower temperature increases the equipment’s thermal efficiency. By adjusting the operating parameters of the equipment, a stable full-section material curtain can be formed inside the drum, making heat exchange more sufficient. The optimized internal lifting board and heat conduction effects are better, effectively eliminating the material sticking phenomenon on the inner wall, and adapting better to moisture and stickiness. The equipment also features relatively low fuel consumption and low drying costs.
The Whole Process
Drying
The coal sludge drying process is: plate frame filter press → conveyor → screw push into the feeding box → rotary dryer → dried conveyor → commodity coal conveyor (blending) → external sales.
Hot Air Flow
Blower → hot blast stove → rotary dryer → pulse bag filter (recovered dust is recycled into the circulating water) → induced draft fan → discharged into the atmosphere through the chimney.
The filter cake of coal sludge treated by the filter press is transferred to the rotary drum dryer by the coal sludge conveyor and drying system conveyor. The dryer is a cylindrical structure with a certain length-to-diameter ratio, and the inner wall is divided into five sections: large angle guide plate, inclined lifting plate, movable grate type wing plate, circular arc lifting plate, and cleaning chain.
After the coal sludge enters the dryer, it is quickly guided to the inclined lifting plate by the large angle guide plate. With the rotation of the drum at 2 to 5 rpm and the 3-5% inclination of the drum itself, the coal sludge is lifted from the bottom of the drum to the top and falls, forming the wet coal sludge curtain. The high-temperature gas generated by the hot blast stove passes through, preheating the wet coal sludge and evaporating some moisture.
When the coal sludge is lifted and dropped repeatedly several times, it moves to the movable grate type wing plate section. The preheated movable grate type wing plate lifts and drops the coal sludge repeatedly, forming heat conduction and convective mass heat exchange with the coal sludge. When the coal sludge moves to the circular arc lifting plate, it compresses the cleaning chain at the lowest part of the drum while transferring the heat received by the chain in the upper space to the coal sludge.
With the continuous rotation of the drum, the coal sludge is lifted, dropped, and fully undergoes mass heat exchange with the hot air. As the drum continues to rotate, the cleaning device cooperates with the circular arc lifting plate to repeat the process of lifting, dropping, cleaning the inner wall of the lifting plate, cleaning the outer wall of the lifting plate, and embedding the cleaning chain in the coal sludge, continuously performing mass heat exchange. The coal sludge moves to the discharge port and is transferred to the conveyor, completing the entire drying process.
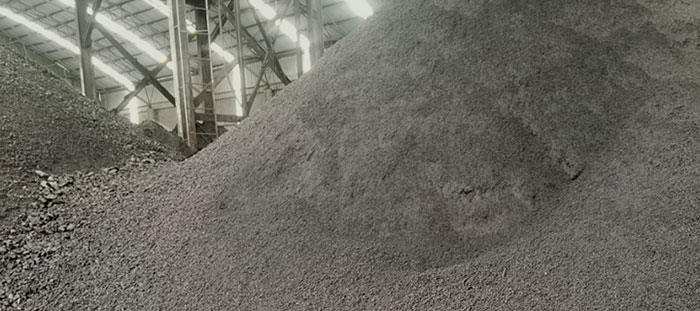
The entire drying process, due to the reasonable design of the structure, does not require a long time.
Types of heat sources
The most common heat source used for the coal sludge has 4 types: coal, gas, steam and oil.
Coal-fired hot air furnaces mainly include automatic chain grate furnaces, pulverized coal furnaces, high and low spray coal furnaces, and high-efficiency fluidized bed furnaces.
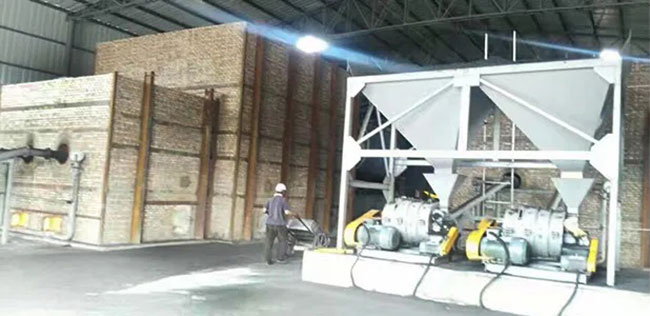
Gas burners mainly include natural gas burners and dual-fuel burners (oil and gas).
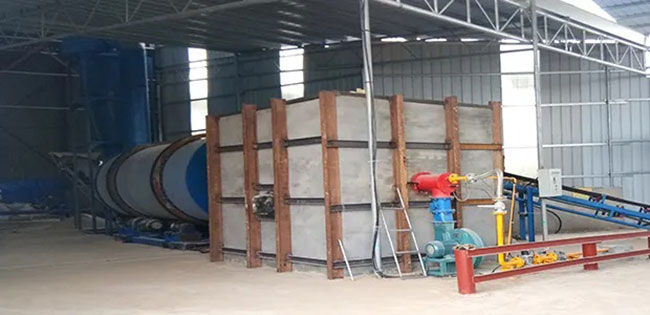
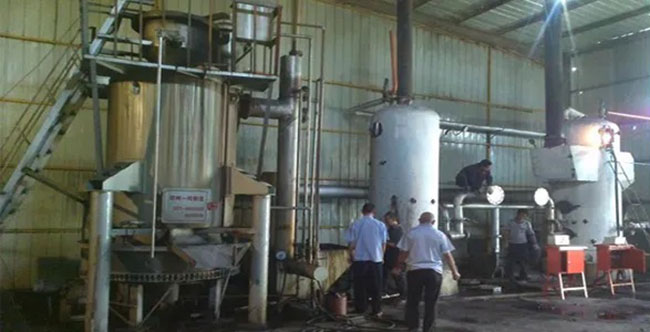
Steam heating sources: The waste heat from steam generated by power plants, boiler plants, brick factories, and other industrial enterprises can be utilized, or heat transfer oil can be used.
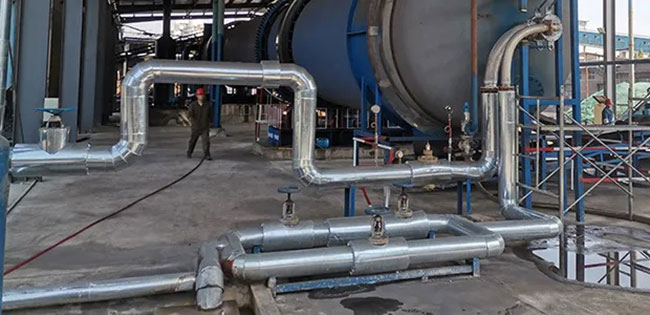
Oil-fired hot air furnaces mainly use various fuel oils.
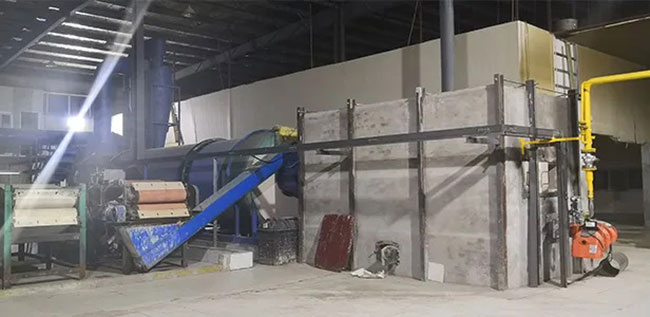
Benefits
Energy Saving
Coal sludge is inherently a sticky fluid with many fine particles. After drying, it mostly forms spherical particles with a diameter of about 1 cm and a moisture content of 8%-12%. It does not need to be crushed and can be directly used as fuel for furnace use, saving the electricity consumption of the crusher (crusher motors are mostly above 200 kW).
Economic Benefit Advantage
As a by-product of coal, coal sludge has a low selling price, generally only 30%-40% of coal’s selling price. After drying, based on a calorific value of 5200 kcal/kg for raw coal and 3800 kcal/kg for coal sludge, drying one ton of wet coal sludge (moisture content 28%) can yield 0.818 tons of dry coal sludge (moisture content 12%). Based on the calorific value, 0.818 tons of dry coal sludge is equivalent to 0.664 tons of raw coal. Drying and using coal sludge can significantly reduce production costs and create good economic benefits for enterprises.
Environmentally Friendly
The application of coal sludge drying technology allows the coal sludge treated by the plate filter press to be directly transferred to the drying system by the belt conveyor. After drying, the coal sludge is stored together with washed coal, ensuring that the coal sludge does not land during the entire processing and external sales process. This once-and-for-all solution completely resolves issues such as land occupation, runoff, and pollution.
The Solution for the Exhaust
In the coal sludge drying process, it generates a large amount of dust, which does not meet environmental standards and has always been a major problem for coal sludge drying. The use of cyclone dust collecting combined with a bag-type pulse dust collector for dust recovery has been shown an efficient way for it.
The recovered dust is recycled and filtered again through a circulating water system. This method has a high recovery rate and good dust removal effect, and it does not produce resource waste during processing. However, for coal with high sulfur content, the exhaust gas generated during the drying process often fails to meet standards. In this case, water dust collecting must be added before exhaust gas discharge to desulfurize the exhaust gas.