Standard for high purity quartz sand
Quartz, scientifically known as a group of minerals composed of silicon dioxide (SiO2), features silicon and oxygen atoms arranged in a repetitive three-dimensional pattern. Silicon dioxide can appear in many different forms and crystal structures, with the most common being quartz, cristobalite, and tridymite. High-purity quartz is a highly refined product obtained from natural quartz minerals through processing and purification, with stringent impurity content requirements, typically less than 50μg/g, and nearly no tolerance for metal ions like potassium, sodium, iron, titanium, or hydroxyl (-OH) groups.
Currently, there is no clear standard for the concept and classification of high-purity quartz. Based on researchers’ viewpoints and current international technology levels, quartz with a purity of ω(SiO2)≥3N-5N and ω(Fe2O3)<10×10-6 can be considered high-purity quartz, while those with 6N-7N can be classified as ultra-high-purity quartz. Quartz sand with a purity of 99.9% can be used to make transparent glass; at 99.99% purity, quartz sand can be used in manufacturing semiconductor filters, liquid crystal displays, and optical glass. Quartz with 99.95% purity is considered low-grade high-purity quartz, 99.99% purity as medium-grade high-purity quartz, and 99.997% purity as high-grade high-purity quartz.
The processing and purification technology of quartz has developed alongside modern industrial needs, making high-purity quartz indispensable in modern industry. It can be used to produce silicon metal, optical fibers, quartz glass, and other high-performance materials, widely applied in electronics, integrated circuits, communication, laser technology, and aerospace industries. The wide range of applications and high added value of processed and purified quartz make it highly valuable.
To obtain high-quality, high-grade high-purity quartz materials, natural crystals are often used as raw materials, which are then purified and processed. However, high-quality quartz raw material resources are limited globally, and the reserves of natural crystals are depleting yearly. The gradual depletion of natural crystal resources at the end of the 20th century and the beginning of the 21st century has promoted the rapid development of high-purity quartz preparation technology using quartzite, silica, and vein quartz as raw materials.
High-purity quartz is initially made from first- and second-grade natural crystals, which are then selected, purified, and processed. The particularity of the formation of natural crystals determines that it has two inherent deficiencies: first, small reserves, poor mining conditions, scarce resources, and high prices, which make it difficult to meet the needs of large-scale industrial production; second, affected by changes in the formation environment, the chemical composition of mineral crystals is unstable, which leads to large fluctuations in the chemical composition of raw materials in large-scale industrial applications, making it difficult to standardize raw materials, and making it difficult to meet the needs of large-scale, stable, high-purity quartz high-end product production.
Deep Processing Technology of Quartz Sand
Physical Methods
1. Magnetic Separation Process
Magnetic separation is a purification method that removes magnetic impurities from quartz minerals through the action of a magnetic field. This process can remove both magnetic impurities and inclusions containing magnetic impurities. Since quartz is non-magnetic, it cannot be magnetized by a magnetic field, while most Fe and Ti impurities are paramagnetic and can be magnetized. Thus, magnetic separation can effectively remove Fe and Ti impurities, achieving high quartz sand content. Magnetic separation is simple and effective for removing magnetic impurities, and it can be divided into strong magnetic separation and weak magnetic separation. Weak magnetic fields remove stronger magnetic impurities like magnetite, while strong magnetic fields remove weaker magnetic impurities like hematite, ilmenite, and garnet.
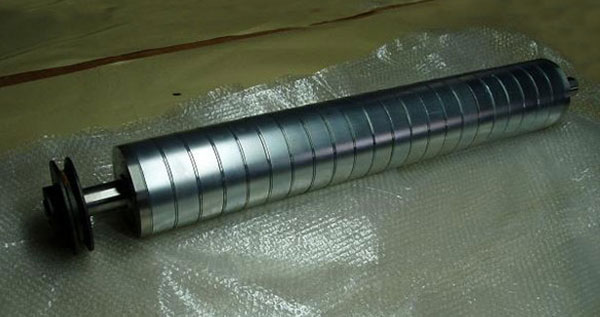
2. Flotation Process
The flotation purification method utilizes the different crystal structures and surface properties of quartz minerals and impurities (mainly feldspar silicate minerals). It employs various collectors or surface activators to adjust the surface characteristics of quartz and impurities, facilitating their separation. Depending on the chosen collectors, flotation can be classified into cationic collector flotation, anionic-cationic mixed collector flotation, and anionic collector flotation. Common cationic collectors include fatty amine collectors, significantly influenced by pH. The most common anionic collectors are oleic acid and sodium oleate, with pure quartz not floating in sodium oleate without the activation of high-valence metal cations. Amphoteric collectors, containing multiple functional groups, exhibit excellent foam performance and combine some advantages of single collectors.
The flotation process can be affected by many factors, such as temperature, choice of flotation reagents, pH control, etc. Before flotation, quartz sand is ground into small particles to allow physical separation of various minerals, and calcination followed by water quenching can improve the flotation effect.
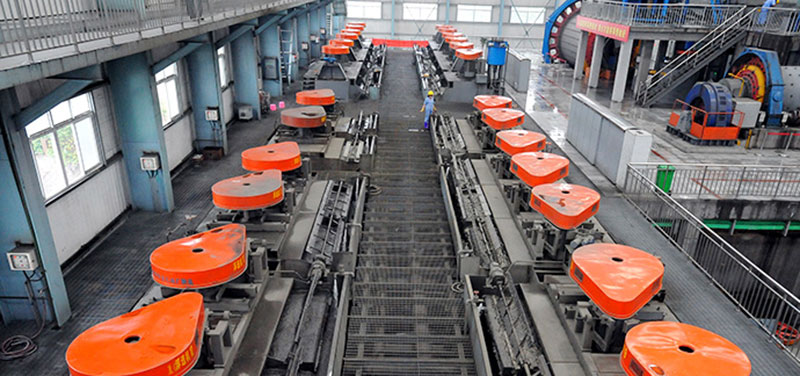
3. Calcination Process
Calcination involves heating quartz to high temperatures, then quenching it in water, which aids in purifying the quartz. This process has two main effects in quartz purification. First, thermal-assisted crushing reduces energy consumption and prevents over-crushing. Second, it facilitates subsequent impurity removal processes by causing abrupt changes in internal stress, creating cracks and exposing inclusions, making impurities easier to remove in later purification steps.
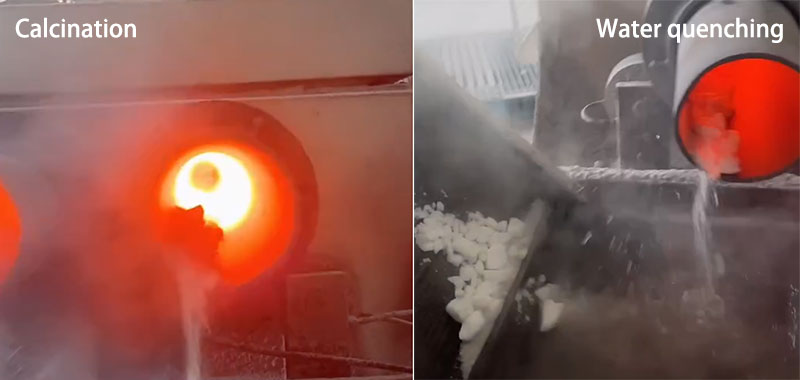
4. Acid Leaching Process
The most challenging impurities to remove from quartz crystals are those directly substituting into the quartz lattice. Physical separation methods like grinding, sieving, density separation, and magnetic separation are ineffective because these impurities are uniformly distributed in the lattice. Since quartz is insoluble in acids other than HF, chemical means can be used to dissolve various metal impurities from the quartz surface, fissures, or structural layers through acid leaching, achieving a higher purification level. Commonly used acids include sulfuric acid, hydrochloric acid, oxalic acid, and hydrofluoric acid. Mixed acid leaching can produce a synergistic effect for better impurity removal, often employing mixed acids for leaching. Factors influencing acid leaching include acid choice, concentration and dosage, solution temperature, leaching time, and stirring, which enhances contact between the acid and quartz surface, improving the purification effect.
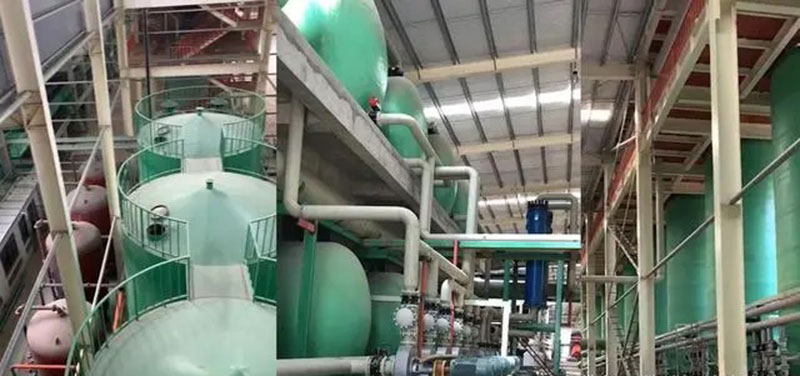
5. Chlorination Roasting Purification Process
Chlorination roasting is a highly effective method for removing lattice impurities from quartz. Under specific temperature and atmospheric conditions, introducing chlorinating agents transforms metal oxide impurities into metal chlorides. Given their generally low boiling points, these chlorides can be volatilized and separated from quartz. During chlorination roasting, the chemical potential gradient between the quartz surface and its interior allows the diffusion and expulsion of inclusions, achieving deeper purification. Common chlorinating agents include Cl2, HCl, NaCl, and NH4Cl. These agents, stronger oxidants than O2 at high temperatures, can chlorinate and remove Al2O3, Fe2O3, and TiO2 impurities. Chlorination roasting offers simple equipment, excellent impurity removal, and high efficiency, making it a highly effective quartz purification method. Additionally, pollutant gases can be treated, such as Cl2 being treated with NaOH, minimizing environmental impact.
6. Hydrometallurgical Techniques
Typically used for leaching and extracting metals from mineral ores, hydrometallurgical techniques can also remove and separate metal minerals from non-metallic ores, especially for iron-containing minerals. In quartz purification, traditional chemical processes include microbial leaching, high-temperature leaching, high-pressure leaching, and catalytic high-temperature leaching. These techniques have introduced new methods for producing high-grade quartz sand and reducing acid consumption. Hydrometallurgical techniques primarily utilize acids to separate quartz and valuable metal elements from impurity minerals. Microbial leaching reduces acid consumption and costs compared to simple acid leaching. High-temperature leaching accelerates leaching through heating, increasing impurity metal element leaching rates. Increasing pressure during high-temperature leaching effectively reduces acid consumption. Introducing stable liquid catalysts in catalytic leaching improves efficiency without using HF, enhancing quartz ore purification.
Microbial leaching offers low cost and pollution, requiring only room temperature for the process. The treated leaching solution can be discharged after simple processing. However, its application is limited by humidity, temperature, pH, water consumption, microbial strains, and leaching methods (dump leaching and tank leaching).
High-temperature leaching is one of the most commonly used techniques, with easy operation and low-cost equipment advantages in industrial production. Leaching temperatures range from 20-100℃, significantly improving leaching speed and rate at low costs. However, acid consumption and pollution from impurity dissolution are major drawbacks.
High-temperature, high-pressure leaching outperforms simple high-temperature leaching, significantly improving purification speed. However, it exposes equipment to a fluorine-rich environment, causing severe corrosion and reducing equipment lifespan. Catalytic high-temperature, high-pressure leaching avoids fluorides, offers simple components, low consumption, reusable leaching agents, and environmental friendliness, yielding excellent purification results.
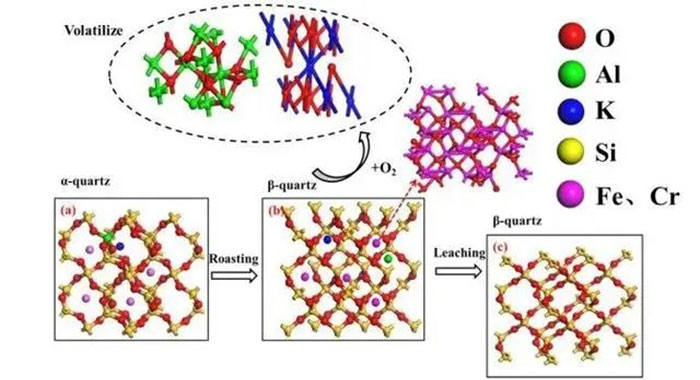
Chemical Methods
Chemical Synthesis
Chemical synthesis of high-purity quartz generally involves direct and indirect methods. Direct methods include chemical vapor deposition (CVD) and plasma-enhanced chemical vapor deposition (PCVD) using silicon halides like silicon tetrachloride. These methods produce synthetic quartz glass with uniformity, high transmittance, and low production costs. However, the process generates toxic, corrosive gases like HCl or Cl2, increasing equipment corrosion and environmental impact. Indirect methods, compared to direct methods, offer doping control (e.g., F, Ti, Al, B, and rare earths) and hydroxyl content control for superior quartz glass properties.
1. Direct Methods
(1) Chemical Vapor Deposition (CVD)
CVD involves the hydrolysis or oxidation of silicon-containing gaseous compounds (e.g., SiCl4, SiH4, and Si4O4(CH3)8) in a hydrogen-oxygen flame, producing SiO2 particles that deposit layer by layer on a rotating substrate to form transparent quartz glass. CVD-produced high-purity quartz features low impurity content and excellent optical uniformity, although high hydroxyl content affects optical properties. CVD quartz glass is widely used in integrated circuits, precision instruments, and military aerospace.
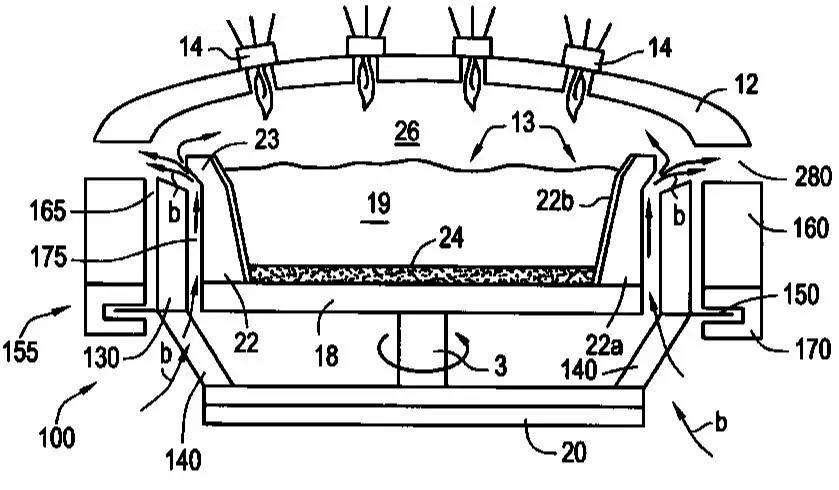
(2) Sol-Gel Method
The sol-gel method converts a solution of silicon alkoxide (e.g., tetraethyl orthosilicate, TEOS) into a gel through hydrolysis and polycondensation reactions. The gel is then dried and sintered to produce high-purity SiO2 powder. The sol-gel method offers fine particle size control and uniformity, enabling the synthesis of high-purity SiO2 powder with specific properties (e.g., low density, high specific surface area, and low impurity content). The sol-gel method is widely used in producing high-performance optical materials and advanced ceramic materials.
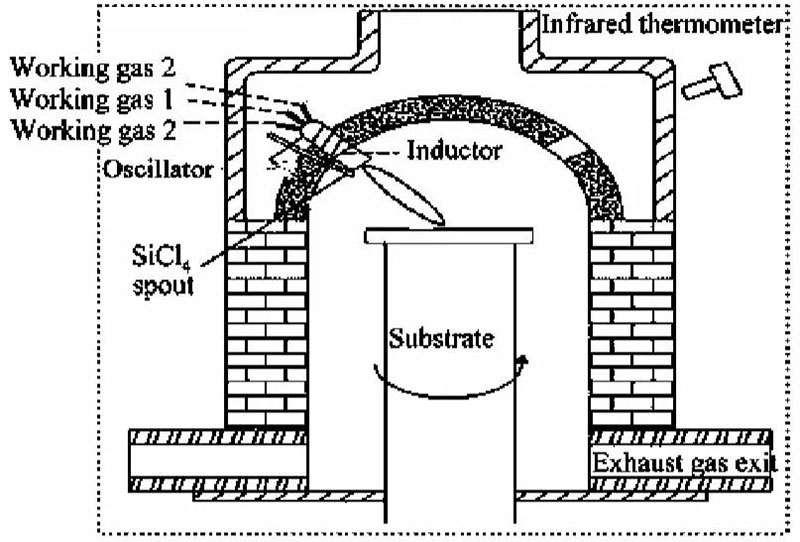
2. Indirect Method
Aerosol Method
The aerosol method converts silicon-containing gaseous compounds (e.g., SiCl4 and SiH4) into fine SiO2 particles through high-temperature pyrolysis or oxidation reactions. The aerosol method offers excellent particle size control and uniformity, enabling the synthesis of high-purity SiO2 powder with specific properties (e.g., fine particle size, high specific surface area, and low impurity content). The aerosol method is widely used in producing high-performance optical materials and advanced ceramic materials.
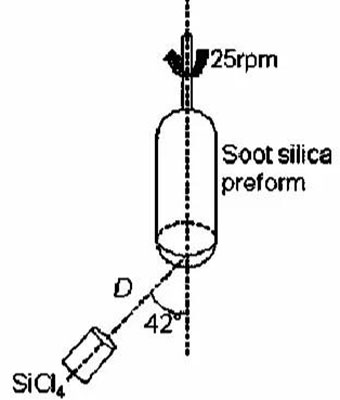
Applications of High-Purity Quartz Sand
Quartz is a fundamental material in industrial production. Its simplest uses include filtration and absorbents, casting sand, fillers, or abrasives. In some high-tech industries, the applications of quartz are also very extensive and important. High-purity quartz, which is of high added value, can be used in the production of optical fibers and monocrystalline silicon for the electronics industry and photovoltaic cells. Another special category includes laboratory glassware for synthesis and analytical chemistry, which also holds considerable value. According to statistics, in the production chain using quartz as a raw material, silicon metal is priced at 255 euros per ton, silicon tetrachloride is priced at 630 euros per ton; high-purity quartz with an impurity content of less than 20 ppm can reach a value of 5000 euros per ton, and ultra-pure quartz used in the electronics industry can sell for up to 80,000 euros per ton.
Quartz glass is an industrial technical glass made by melting a single component of silicon dioxide. It is high-temperature resistant, has a low coefficient of expansion, thermal shock resistance, excellent chemical stability, and superior electrical insulation. With the advancement of science and technology, high-purity quartz is widely used in high-tech industries such as fiber optic communications, solar photovoltaics, aerospace, electronics, and semiconductors. The excellent performance of quartz glass mainly depends on its purity. High-purity quartz sand, with high purity and low impurity content, is the best raw material for manufacturing high-performance quartz glass.
High-purity quartz sand plays a crucial role as the primary raw material in glass batch mixtures, accounting for 60%-80% of the mixture. The quality of the glass batch not only affects the quality of optical glass products but also impacts the service life of glass melting furnaces. The use environment of optical glass products requires very high standards for impurity content, refractive index, light transmittance, and microscopic defects. All these factors strictly demand high-quality quartz sand as the main raw material. For high-precision, high-resolution optical glass, high-purity quartz sand is an excellent raw material.
Semiconductor Industry
The semiconductor industry is the foundation of the global information industry. The widespread application of semiconductor products has driven the advent of the information and intelligent era. The most commercially valuable in semiconductors are silicon and some of its binary compounds, such as silicon carbide. These high-performance materials are widely used in the electronic information field, being manufactured into various high-tech products like chips with excellent performance. Every year, chip manufacturers and designers significantly improve the performance of their products, and the reduced prices make high-tech products increasingly accessible to consumers. The global semiconductor industry showed a yearly increasing trend from 2012 to 2019. In this field, high-purity quartz is used to produce higher-performance elemental silicon and other compound materials, which are widely applied in the semiconductor field.
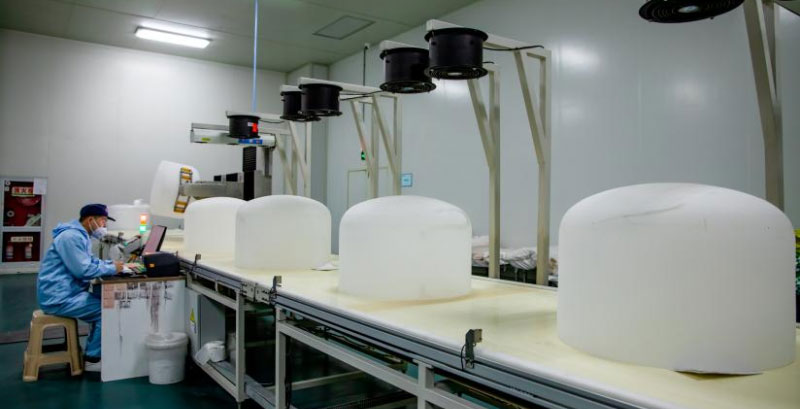
Optical Fiber
Quartz glass can be used to manufacture optical fibers, which are very fine strands with a diameter of less than 8 millimeters. Digital data is transmitted through optical fibers in the form of light. Optical cables made of optical fibers play an irreplaceable important role in modern communication transmission. Moreover, high-purity quartz also has certain optical properties; it can form polarized laser beams and, using high-purity quartz as a window, can manufacture fiber lasers with prisms, filters, and timing devices. High-quality quartz crystals are also used for prisms and lenses in optical instruments. Thus, optical fibers made from high-purity quartz raw materials have very high added value.
Solar Cells
The solar energy industry is a very hot high-tech industry, with the annual output of solar cells increasing year by year. China has also invested heavily in the photovoltaic industry. Producing solar cells requires a large amount of high-purity quartz. In a modern society advocating green energy, the demand for solar cells is very high, so the demand for high-purity quartz in the photovoltaic industry is also enormous. The solar-grade silicon produced from high-purity quartz is of considerable added value; for example, the solar-grade silicon produced by Siemens and its subsidiaries can sell for up to 40 euros per kilogram.
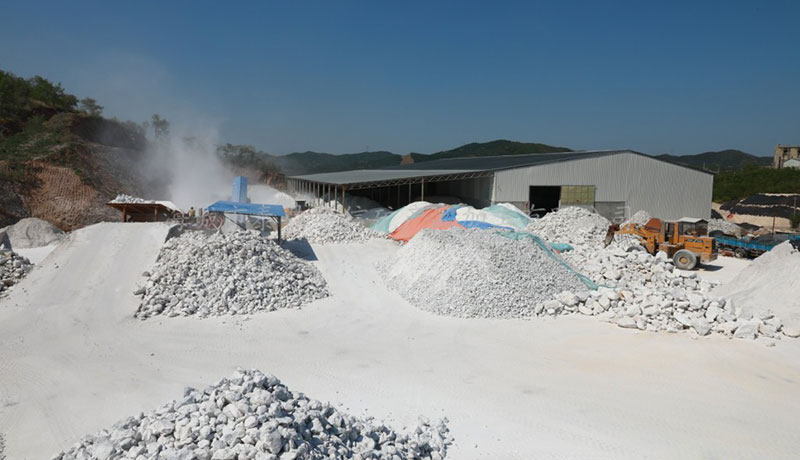
In summary, high-purity quartz sand is a critical material in various high-tech industries, ranging from semiconductors to solar cells, owing to its exceptional purity and minimal impurity content. Its applications significantly contribute to advancements in technology and the production of high-performance products.