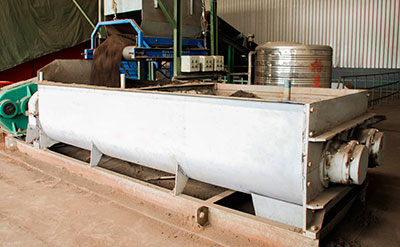
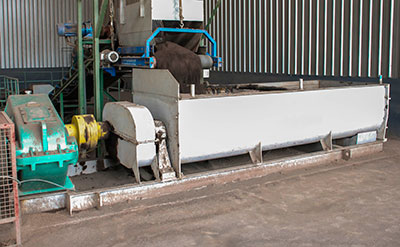
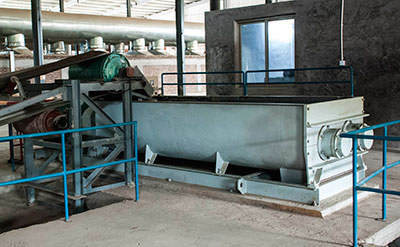
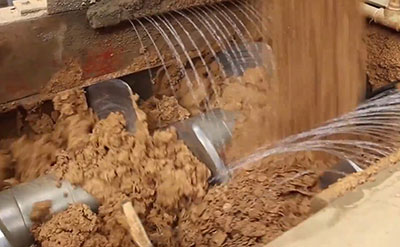
Pugmill mixer also named as double shaft mixer or twin shaft mixer, is a kind of continuous blender which mixes, kneads and moistens the mixture to optimize the blending and disintegrating effect.
The forward and reverse alternating screw paddles are used to make the materials advance alternately in the ω-shaped mixing tank, which has the characteristics of strong mixing ability and uniform feeding. It is suitable for mixing and humidification of loose materials, such as coal humidity control, and can also be used as a pretreatment equipment before intensive mixing.
A pair of mixing shafts is intalled in the mixing tank, which are the active mixing shaft and the passive mixing shaft. The two ends of the mixing shafts are supported by the front and rear bearing seats, and the two ends of the mixing tank are respectively sealed by the sealing seat.
Mixing paddles are installed on the shaft according to the direction of screw propulsion, and the rotation directions of the two shafts are opposite. When the material is rotated by the mixing paddle, it is mixed and moved forward. The uniformity and residence time of the material mixing mainly depend on the angle between the paddles and the shaft and the rotation speed of the shaft.
The material is fed from the top of one end of the mixer. When the two horizontal shafts rotate, because the paddle is installed at a certain angle, the paddle on the shaft rotates in a screw shape, pushing the material forward along the shaft, and the shafts rotate together to drive the stirring and pushing of the paddles. Rolling up and down and moving left and right by extrusion, the material is gradually mixed evenly, and moves to the discharge end, and finally discharges at the lower opening at the other end.
Equipment equipped with the liquid adding device will add liquid when the material enters the mixing chamber, and fully wet and mix it during the mixing process.
1. Transmission part 2. Feeding port 3. Paddle 4. Mixing tank 5. Twin shaft 6. Frame
The mixing is transmitted from the transmission wheel to the main shaft through the pin coupling. The special shaft mixing paddles welded or equipped on the main shaft rotates synchronously, turning the material evenly in the mixing tank, making the material fully mixed. Thus greatly reducing the residual amount of the material.
The transmission is driven by the motor to drive the pulley, V-belt, reducer, etc. to make the main shaft rotate. The reducer and the working section of the main engine are made of nylon pins as the transmission joint, and are driven by the transmission mechanism, which is convenient for assembly and maintenance.
The force from the gear motor through the coupling is transmitted to the cylindrical gearbox, which transmits rotation to the mixer shafts. The drive system allows you to compensate for possible misalignment of the shafts due to installation errors, under shock, vibration and dynamic loads, guarantees high torque on the mixer shaft and overall reliability of the equipment.
All working parts of the machine are installed and fixed on the frame, and the frame is welded with thick steel plate and channel steel.
Mixing and blending: FGD scrubber sludge, fly ash, and lime for SO2 neutralization, municipal sludge for composting facilities, pigments and dyes, and other processes combining moist and dry feed materials, gangue, shale, tailings, construction waste, clay and fly ash mixing for clay and tile making.
Agglomeration and dedusting: Granulation of agricultural chemicals, fertilizers, chemical consumer products, carbon powders, flue dust from dust collectors in power plants, animal feed, cement pelletizing pre-agglomeration, etc.
Material conditioning: Fly ash, cement or lime kiln dust, foundry dust, iron oxide, friction material waste, lead fume, zinc oxide, copper reverts and concentrates.
Model | Rotating diameter (mm) | Mixing length (mm) | Capacity (m3/h) | Power (kW) |
MTS0432 | 450 | 3200 | 15-20 | 15-18.5 |
MTS0540 | 530 | 4000 | 30-40 | 18.5-22 |
MTS0640 | 630 | 4000 | 50-70 | 22-30 |
MTS0740 | 750 | 4000 | 70-80 | 30-37 |
MTS0940 | 900 | 4000 | 110-130 | 55-75 |
MTS1140 | 1100 | 4000 | 190-210 | 75-90 |
MTS1250 | 1200 | 5000 | 250-280 | 2*55 |
MTS1350 | 1300 | 5000 | 320-350 | 2*75 |
MTS1450 | 1400 | 5000 | 450-540 | 2*90 |
MTS1562 | 1500 | 6000 | 550-650 | 2*110 |
Why Using Intensive Mixer in Sintering System The sintering production process primarily…
Mixing and pelletizing processes are very important steps in the sintering production…
With the intensification of the energy crisis, coal prices have risen sharply. At…