Mixing and pelletizing processes are very important steps in the sintering production process. Mixing is the careful blending of various components in the batching process, while pelletizing is turning the materials into a suitable particle size with good permeability.
The purpose of mixing and pelletizing
- To blend the various materials prepared in the batching room to obtain a relatively uniform mixture.
- To add the necessary moisture to the sintering mixture during the mixing process, making the sintering mixture wetted by water.
- To pelletize the sintering material to obtain a mixture with a suitable particle size and good permeability.
Mixing and pelletizing ways
According to the number of mixing stages, there are one-stage, two-stage, and three-stage mixing and pelletizing processes. The one-stage mixing and pelletizing process uses one drum machine to complete the blending and pelletizing of fine particles. This process was used in early sintering production and primarily used coarse powder ore as raw material. The two-stage mixing and pelletizing process generally consists of two drum mixers and a belt conveyor. The first mixer mainly completes the blending of the sintering material, while the second mixer mainly completes the pelletizing of the mixture. The three-stage mixing and pelletizing process was gradually adopted with the development of large-scale sintering machines and the need for enhanced thick-layer sintering techniques. As the related mixing technology advances and the particle size of sintering raw materials decreases and the variety of raw materials increases, some sintering plants have begun to use intensive mixers to replace the first-stage drum mixer. In the second-stage pelletizing, two or more smaller drum mixers are sometimes used to replace a single large drum mixer.
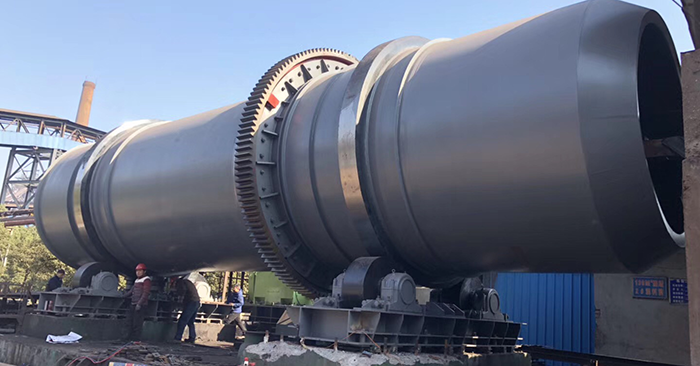
Two-stage drum-type mixing and pelletizing
The conventional mixing and pelletizing process is as follows: all materials are added to the mixture belt conveyor in the batching room according to a certain ratio, then fed to the first mixer by the belt conveyor. Water is added in the first mixer to mix the materials evenly. After that, the materials enter the second mixer for pelletizing. The second mixer is generally composed of a drum mixer. The materials are pelletized into 3-5mm balls in the second mixer, and water is added to further adjust the moisture content of the mixture, forming suitable particle sizes. The mixture after the second mixing is directly sent to the sintering machine for sintering operations.
This configuration of the mixing and pelletizing process is the most common and is used in most sintering plants.
Three-stage drum mixing and pelletizing process
In some large sintering plants, to further extend the pelletizing time, the mixing and pelletizing process is set up as a three-stage configuration. The first stage is for blending the sintering mixture, and the second and third stages are for pelletizing. All materials are proportioned in the batching room and enter the first mixer. After the first mix, the materials enter the second and third mixers for pelletizing. The mixture after the third mix is directly sent to the sintering machine. The difference between the conventional two-stage and three-stage processes is an additional pelletizing stage. If the pelletizing time is sufficient, a two-stage configuration can meet production requirements. Otherwise, an additional pelletizing stage should be added to extend the pelletizing time and achieve the desired pelletizing effect.
Mixing and pelletizing process with intensive mixer
In sintering engineering, with the increase in the proportion of concentrates and the addition of various other iron-containing materials, higher requirements are placed on material mixing. Therefore, an appropriate mixing and pelletizing process and equipment are needed. Intensive mixer are generally used to replace the first-stage drum mixer. The mixing and pelletizing process using intensive mixer can also be divided into two-stage and three-stage processes. Intensive mixer are usually used as the first-stage blending equipment, while drum mixers are used for pelletizing in the second and third stages. In the two-stage mixing and pelletizing process with intensive mixer, the second stage drum mixer can either be a single large drum mixer or multiple smaller drum mixers arranged in parallel. The three-stage mixing and pelletizing process uses an intensive mixer for the first stage blending, and drum mixers for pelletizing in the second and third stages.
Due to the structural form of intensive mixer, with rotors equipped with ploughs inside, the service life of the ploughs is significantly affected by the sinter return fines. Therefore, considering the maintenance issues of intensive mixer, return fines do not directly enter the intensive mixer but are added to the belt conveyor after intensive mixing, then enter the subsequent pelletizing stages. Alternatively, a bypass can be set up at the intensive mixer so that when the intensive mixer is under maintenance, the material bypasses the intensive mixer and directly enters the subsequent mixers.
HPS (Hybrid Pelletized Sinter, two-stage drums one-stage disc) mixing and pelletizing process
HPS mixing pellet sintering, belonging to the mini pellet sintering process, mixes iron ore fines, return fines, fluxes, and fuel with water to form mini pellets with a diameter of 5-10mm. These mini pellets are coated with a certain proportion of solid fuel on the surface before sintering. Compared with conventional sintering, the mini pellet sintering process includes additional steps of enhanced pelletizing and outer rolling of carbon powder.
Enhanced pelletizing involves adding a disc pelletizer between the first and second mixing stages to form mini pellets of 5-10mm. The fuel is divided, with 20%-30% added in the batching room (internal carbon material), and 70%-80% (external carbon material) added after pelletizing. The external carbon material coats the surface of the green pellets, changing the combustion conditions during sintering, improving bed permeability, increasing production capacity, and reducing fuel consumption.
The role of external carbon material is twofold: first, to evenly and firmly adhere the external carbon material to the green pellet surface, and second, to make the green pellets smoother after a period of rolling, further improving bed permeability.
MPS (Micro-Pelletization and Sintering, three-stage drums) mixing and pelletizing process
The MPS process involves adding external carbon material (70%-80%) in the final stage of the three-stage drum mixing and pelletizing process. The first stage mixes the materials, the second stage pelletizes the materials into mini pellets, and before the third mixing stage, fine coal powder is added proportionally. The third stage is a rolling machine where coal powder coats the mini pellets, compacting and adhering the coating firmly. The mixture from the third stage is directly sent to the sintering machine. This process improves bed permeability, increases bed height, enhances sinter strength, increases utilization rates, and reduces fuel consumption.
Comparison of mixing and pelletizing processes
- When using powder ore for sintering or when the concentrate ratio is not high, the two-stage drum mixer mixing and pelletizing process can meet production needs. The drum mixer has a simple structure, reliable operation, and is a common configuration in current sintering plants.
- In large sintering plants, to extend pelletizing time, a three-stage mixing and pelletizing process is adopted. The first stage uses a drum mixer for blending, and the second and third stages use drum mixers for pelletizing to meet the pelletizing time requirements. Compared to the two-stage drum mixing and pelletizing, the three-stage configuration effectively improves particle size distribution and reduces the proportion of particles below 3mm.
- With the application of intensive mixer in sintering, some plants use intensive mixer to replace the first mixer, while the pelletizing stage still uses drum mixers. The mixing effect of intensive mixer is better than drum mixers, but intensive mixer have higher maintenance frequencies. Therefore, in this process configuration, material bypass is generally considered. When the intensive mixer is under maintenance, the material bypasses the intensive mixer and goes directly to the subsequent mixers; or return fines do not enter the intensive mixer but are added to the belt conveyor after the intensive mixer, avoiding excessive wear on the ploughs and thus reducing maintenance frequency.
- Under high concentrate ratios, conventional two-stage mixing and pelletizing cannot meet the requirements. Enhanced pelletizing measures are needed to ensure pelletizing effects. Therefore, mini pellet sintering methods can be used to improve pelletizing effects, such as the HPS (two-stage drum one-stage disc) mixing and pelletizing process or the MPS (three-stage drum) mixing and pelletizing process, i.e., one stage of mixing, two stages of pelletizing, and three stages of external rolling with coal.
Research results show that when pelletizing time is less than 8 minutes, the MPS process has better pelletizing effects than the HPS process. Its corresponding sintering speed, utilization rate, and sinter drop strength are also better. When the pelletizing moisture is 7.0%, the MPS process outperforms the HPS process in all indicators. Both the MPS and HPS processes can form ferrite well, but the MPS process produces sinter with higher calcium ferrite content, with more ideal crystal formation, strength, and reducibility. In plant production, the MPS process can replace the HPS process. Both the HPS and MPS process configurations have better pelletizing effects, sinter quality, sinter mineral phase, and metallurgical properties than conventional sintering methods. In these process configurations, intensive mixer can also replace the first-stage drum mixer.
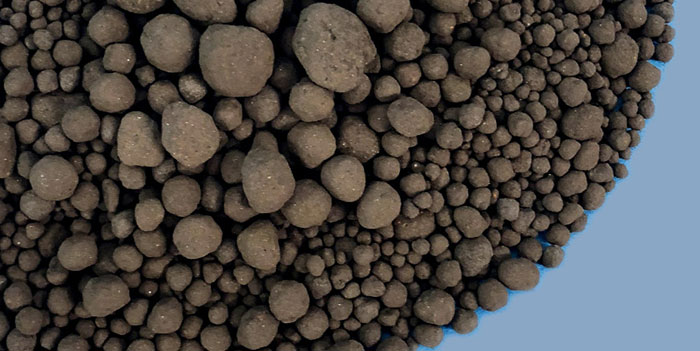
Mixing and pelletizing equipment
Common mixing and pelletizing equipment used in the mixing and pelletizing process includes drum mixer, intensive mixer, disc pelletizer, etc.
Drum mixers have a simple structure, large production capacity, convenient operation and maintenance, and high equipment utilization rates, with mixing effects slightly lower than intensive mixer.
Intensive mixer have a smaller size than drum pelletizers, better mixing effects, and lower energy consumption per unit than drum mixers. However, intensive mixer have lower equipment utilization rates than drum mixers, especially since the cold return fines in the mix greatly affect the plough’s service life, requiring frequent replacement. Therefore, when using intensive mixer, a bypass system is generally set up to ensure.
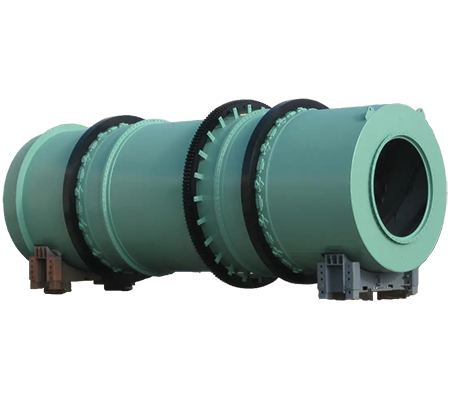