What is potassium nitrate
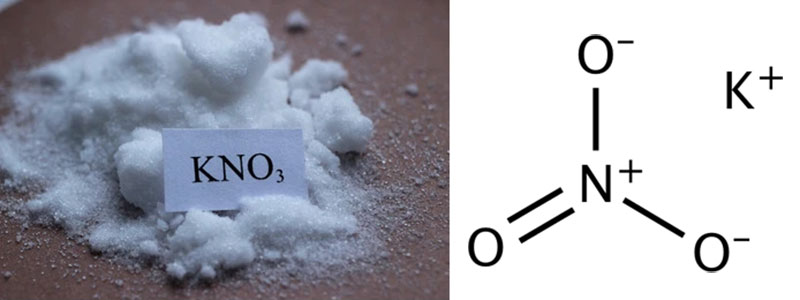
The application of potassium nitrate
Pharmaceutical industry: manufacturing penicillin potassium salt, rifampicin, diuretic, diaphoretic and cooling agents;
Agriculture: used as potash and nitrogen fertilizer;
Ceramic industry: ceramic color(ant);
Machinery industry: metal quenching salt bath agent;
Food industry: meat preservatives;
Mining industry: beneficiation agents;
Glass industry: clearing agent
etc.
Why make potassium nitrate granular
Due to the influence of crystal shape, composition, structure, surface area, physical and chemical properties and surrounding storage environment, potassium nitrate is easily agglomerated, which brings difficulties to storage, transportation and use. Granulation to produce granular/pellet potassium nitrate products is the most effective way to prevent potassium nitrate caking.
Granulation greatly reduces the contact area between particles, fundamentally improves the flow performance and storage and transportation performance of potassium nitrate products, makes potassium nitrate transportation, storage and use very convenient, and completely solves the problem of potassium nitrate agglomeration that troubles production companies and users.
Granulation greatly reduces the contact area between particles. Fundamentally improve the flow performance and storage and transportation performance of potassium nitrate products, It makes the transportation, storage and use of potassium nitrate very convenient. It completely solves the problem of potassium nitrate agglomeration that troubles manufacturers and end users.
In addition, when used as fertilizer, granular/pellet potassium nitrate dissolves slowly and has the effect of a slow-acting fertilizer, which can improve the effective utilization of fertilizer by crops and has strong market competitiveness. Therefore, the granulation of potassium nitrate products is an inevitable trend in production.
Dry granulation of potassium nitrate
The potassium nitrate dry material is aggregated into dense and hard flakes under the pressure of the counter-rollers, which is called compaction. The flakes are then crushed and screened to become granular materials, which is called granulation. Compaction is to squeeze out the air between particles, and to make the distance between particles close enough to generate attractive forces such as van der Waals force, adsorption force, crystal bridges and embedded connections. Unqualified large particles and fine materials are returned to the roller compactor for re-granulation. Compacting granulation mainly relies on the particle strength formed by the force between molecules.
Process
Raw material – potassium nitrate compactor – crushing – screening – finished product (2-4mm) – packaging
Advantage
- Low energy consumption. No drying required.
- Lower investment.
- Flexible raw material composition.
- Suitable for a wide range of raw material particle sizes.
- Backflow material ratio is low. Accounting for about 35-50% of the total feed volume of the compactor, the process is simple.
- Low processing cost, especially suitable for heat-sensitive materials.
- The apparent density of the product can be increased by 1.5 to 3 times.
Disadvantage
- Smaller capacity.
- The shape of the product is irregular particles.
- Due to the crushing process in production, dust is generated.
Making potassium nitrate from a wet process
Grind the potassium nitrate dry material and granulating agent directly and add them to the pelletizing tray, and spray an appropriate amount of water to control the pellet moisture.
After the raw material pellet core enters the pelletizing disk, it moves along a parabola under the action of centrifugal force, friction and gravity in the disk. Due to the adhesiveness and plasticity of the material, the cores bond with each other and gradually grow during the movement.
When the parameters such as the inclination angle of the balling disk, disk edge height, rotation speed and moisture content are constant, the balls of different particle sizes leave the disk edge and roll downward at different breakaway angles due to different gravity. During the continuous rolling process of the ball, the water in the ball is continuously squeezed out of the surface.
Due to the adhesion of the material and the natural volatilization of the surface liquid film, the material ball has a certain strength, and then is discharged from the edge of the plate as the tilting plate rotates. After drying, potassium nitrate pellet is obtained.
Process
Raw material and additive along with water – pelletizing (potassium nitrate pelletizer) – drying (belt dryer) – cooling – screening – finished product – packing
Advantage
- Lower energy consumption.
- The achieving rate is high and the dust in the production process is small.
- The process flow is relatively simple.
- Low investment, intuitive operation and easy maintenance.
- The product is approximately spherical, with rounded particles and high strength.
Disadvantage
- Equipment installation and debugging are complicated, and the capacity for one machine is small.
- Additional drying and cooling facilities are required.
- Binder needs to be added to assist in granulation, thereby affecting product purity.
Comparison and the cost/price
The choice of potassium nitrate granulation method depends on the different uses of the product.
When the product quality requirements are relatively high, it is difficult to produce granular by disc pelletizer, so roller compaction is appropriate. When the product quality requirements are relatively low, faster pelletizing via discs can be used.
Of course, the choice of potassium nitrate granulation process also needs to be considered from aspects such as investment, production capacity and energy conservation to maximize profits.