What is coke fine
Coke fine refers to the small-sized particles or fine granules of coke, a carbon-rich material derived from coal or petroleum. These fine particles are typically produced as a by-product during the crushing, screening, and handling of larger coke pieces.
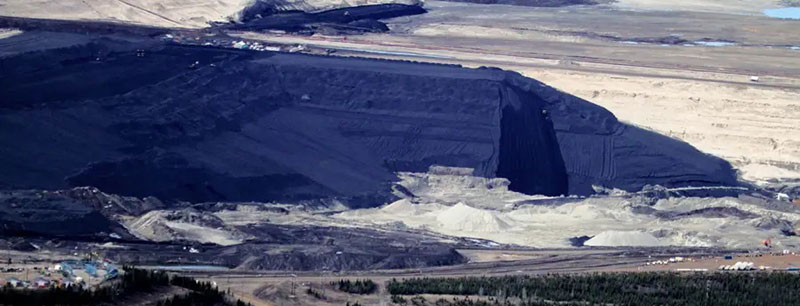
Coke fine sources – types of them
At present, coke fines primarily come from the following two types of coke:
Coal Coke
Coal coke is a solid carbonaceous product obtained from the pyrolysis of high volatile coal at medium to low temperatures (450°C to 900°C). The coal pyrolysis process involves heating coal products in an oxygen-free (or air-isolated) environment, causing a series of complex chemical reactions and physical changes at various temperature conditions.

Petroleum Coke
Petroleum coke, also known as petcoke, is a product derived from the thermal cracking process of heavy oil after separating light and heavy oil fractions through crude oil distillation. The primary element composition of petroleum coke is carbon, which accounts for over 80wt%, with the remaining elements being hydrogen, oxygen, nitrogen, sulfur, and metal elements. It appears as irregularly shaped, metallic lustered, black or dark gray porous solid particles with a well-developed porous structure. The main component of petroleum coke is carbonaceous material.
Petroleum coke is a byproduct of the oil refining industry. During oil refining, delayed coking units are used to conduct high-temperature deep thermal cracking and polycondensation reactions on petroleum residue, producing coking gas, coking naphtha, coking diesel, coking wax oil, and petroleum coke. This process converts low-cost oil products mainly into high-value liquid oils and gases, with petroleum coke being a byproduct of the entire refining process. Various impurities in crude oil and catalysts used during the refining process ultimately remain in the petroleum coke, among which sulfur content, as a harmful substance, is a crucial indicator of petroleum coke quality.
Why Make Coke Briquettes
Coke powder possesses excellent characteristics such as low phosphorus, high reactivity, and high specific electrical resistance. Additionally, coke powder is inexpensive and has wide applications in industries such as ferroalloys, calcium carbide, fertilizer production, and blast furnace injection. However, coke powder has poor strength, crush resistance, and plasticity, and the pyrolysis process often results in small particle sizes that are difficult to meet production needs and be used directly.
Currently, forming coke powder into briquettes is an internationally recognized effective method to enhance the application value of coke powder and make rational use of coke powder resources. By adding appropriate additives, the strength, crush resistance, and plasticity of the briquettes can be significantly improved.
Using coke powder as the primary raw material and processing it through various methods to produce briquettes of a certain size and strength, it can be used in fields such as metallurgy, industrial or domestic block fuel, and gasification feedstock. Depending on the raw material, the production process of briquettes, both domestically and internationally, mainly falls into two categories: hot-pressed briquettes and cold-pressed briquettes.
Due to the lack of inherent binding properties in coke powder, binders are typically added, and the mixture is cold-pressed to form briquettes. Under the action of mechanical force, the material and the binder come into close contact, with the binder forming a colloidal or crystalline structure on the surface and in the gaps of the coke powder particles, thus imparting high strength to the briquettes.
A Binder Way
During the coking process, aromatic compounds, benzene series compounds, and anthracene and phenanthrene compounds with adhesive properties are released in large quantities, resulting in very poor adhesion of coke powder. Without adding a binder, briquettes cannot be formed and the coke powder can only be disposed of cheaply as low-grade fuel, causing significant waste. Therefore, adding a binder during the formation of coke powder is a widely accepted practice.
Different Binders
The choice of binder is crucial for the shaping of coke powder. During the preparation process, the binder decomposes under heat into viscous liquid substances (colloids), which bind the coke particles and participate in forming a carbon skeleton, thereby enhancing the overall integrity and strength of the product. Currently, binders can be classified into three main categories: inorganic binders, organic binders, and composite binders. The inorganic content of these binders affects the ash fusion point, adhesion, and slagging properties of the formed coke.
Inorganic Binders
Inorganic binders include bentonite, slaked lime, and clay. Typically, the inorganic binder, water, and coke powder are mixed, and the hydration reaction between water and the binder binds the coke powder. The characteristics of inorganic binders are their wide availability, low cost, and the high thermal strength of the formed coke. However, inorganic binders do not burn or generate heat, and their use in large quantities increases the ash content of the briquettes and reduces their adhesiveness. Additionally, they have poor adhesion in cold states, limiting their application.
Organic Binders
Organic binders include emulsified asphalt, starch, tar, tar pitch, humic acid, calcium lignosulfonate, biomass, wood cellulose, and paper pulp waste liquid. Organic binders have strong affinity and can achieve adhesion with coke powder in small amounts. When mixed and combusted with coke powder, they produce little residual ash. After being dried and cured under external pressure, they can impart certain cold compressive strength to the formed coke.
However, organic binders are relatively more expensive than inorganic ones. They decompose easily under high temperatures, resulting in poor strength of the carbonized product. Hydrophobic organic binders such as tar and asphalt can produce large amounts of smoke during combustion. Additionally, the high sulfur content in petroleum asphalt can cause environmental pollution.
Composite Binder
Composite binders are made from two or more types of inorganic and organic binders, combining the advantages of both. They not only provide higher compressive strength, thermal stability, and cold-state strength to the formed coke but also make rational use of resources and maximize their residual value.
The coke briquetting plant
A typical coke briquetting process is shown as below:
The description
The coke powder is measured and fed into a horizontal double-shaft paddle mixer through a feeder, while the prepared binder is accurately sprayed into the continuously stirred coke powder via a conveying pump and pipeline. During the mixing process, water is consistently injected through another pipe to maintain the moisture content of the raw materials. After output from the paddle mixer, the material will be mixed in an intensive mixer to make it uniformly mixed. Then the mixture will be quantitively sent to the roll briquette machine or an extrusion machine by a feeding machine.
The briquette will be obtained after going through the briquette machine. The briquettes can be sieved, with undersized pieces being returned to the feeding silo. Appropriately sized briquettes are transported to the drying machine by a conveyor, where they are dried to remove any free water. The finished briquettes are ready for use after drying.
Core Equipment in Coke Briquetting Plant
Mixer
The mixer is a crucial component in the briquette production process, akin to the throat for humans. It ensures the system runs smoothly and significantly impacts the strength of the briquettes. When selecting equipment for compressed pellet production lines, it is essential to consider more than just the mixer’s capacity. Factors such as mixing effect and quantitative feeding are also critical.
Mixers can be classified into batch type and continuous type. Here are some tips for choosing the right mixer:
- For large briquette plants, opt for a continuous mixer.
- Choose a suitable type based on the space available.
- Intensive mixing is crucial for uniform binder distribution, reducing binder costs, and improving briquette quality.
- An intensive mixer is recommended for the primary mixing task, whether continuous or batch mixing is required.
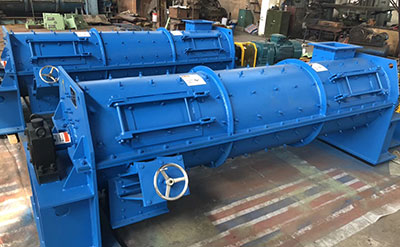
Briquette Machine
The coke fine briquette machine is the key equipment in the coke briquetting system, determining the actual capacity of briquettes produced by the production line. Generally, there are two options: a roller briquette machine or an extruder.
Given the importance of the briquette machine in the coke briquetting plant, it must be selected based on the raw material characteristics, compatibility with the binder, briquette strength requirements, and investment budget. Different models with varying pressures and configurations should be chosen accordingly.
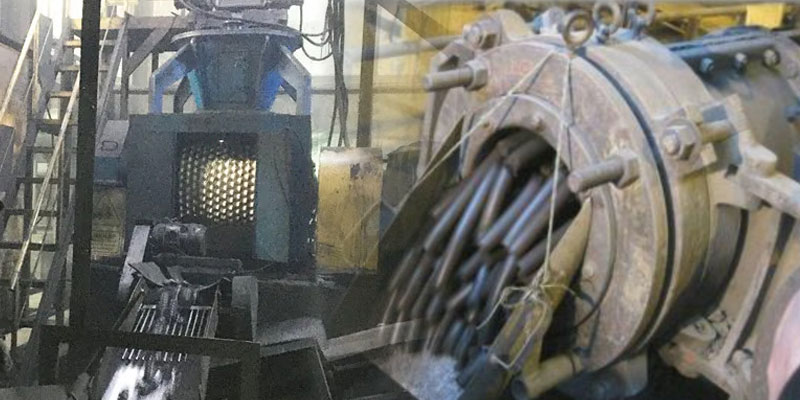
Main Briquetting Process Conditions
Pressure
Increasing the briquetting pressure reduces briquette porosity, increases density, and enhances the contact surface area between raw material particles. This improves the bonding strength between solid particles and the friction between them, resulting in stronger briquettes. Higher pressure also strengthens the molecular bonding between raw material and binder, further enhancing briquette strength.
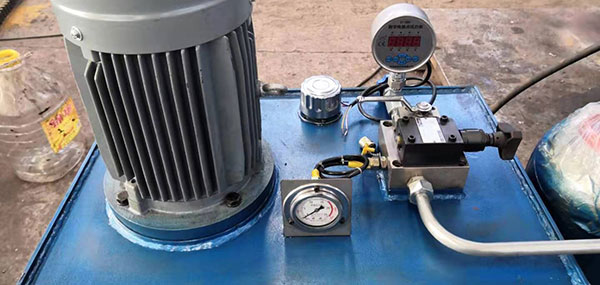
Moisture
Moisture content significantly influences the briquetting process. Proper moisture helps particles rearrange under pressure, fills gaps between particles, and reduces friction, making the particles more compact.
Water acts as a lubricant between the raw material and the roll, reducing pressure loss due to friction. It forms adsorbed and film water on particle surfaces, producing molecular binding force and capillary force, both of which improve briquetting performance.
Suitable moisture levels are critical. Low moisture results in poor particle infiltration, high friction, and reduced briquette strength. Excessive moisture prevents close particle contact and diminishes capillary force, also leading to weaker briquettes.
By carefully managing briquetting pressure and moisture content, you can optimize the quality and strength of coke powder briquettes in your production process.