What is a rotary dryer
The main body of the rotary dryer is a slightly inclined (or sometimes horizontal) rotating cylinder. Wet materials are fed into one end and are dried as they pass through the cylinder, effectively contacting the hot air or heated walls inside. The rotary dryer is a device that simultaneously provides high-temperature heating and conveying. It is widely used in industries such as food, chemical, metallurgy, and building materials. Practical dryers have a minimum diameter of about 0.5 meters and can exceed 3 meters. The shortest length is around 2 meters, while the longest can reach up to 50 meters.
Advantages and disadvantages
Compared to other drying equipment, rotary dryers have several advantages:
- high production capacity and continuous operation.
- simple structure and easy operation.
- low failure rate and low maintenance costs.
- wide application range.
- low fluid resistance.
- suitable for drying granular materials and beneficial for materials with high adhesion.
- large operational flexibility allows for significant product flow fluctuations without affecting quality.
- easy cleaning.
However, it also has disadvantages:
- large equipment size.
- high initial investment; difficult installation and disassembly.
- significant heat loss.
- low thermal efficiency (except for steam tube rotary dryers).
- long material residence time within the dryer, with a wide variation in residence time among different material particles.
Types
To improve drying performance, the development trend of rotary dryers is to develop new equipment with combined devices by setting up paddles of different geometric shapes. Based on the heating method of the dried material, rotary dryers can be classified into five types:
- direct heating
- indirect heating
- combined heating
- steam calcining
- spray granulation
Direct Heating Rotary Dryers
In this type of dryer, the heat carrier directly contacts the dried material, primarily using convective heat transfer. They are the most widely used and are divided into three types: conventional direct heating rotary dryers, blade-through-flow rotary dryers, and ventilated rotary dryers.
In conventional direct heating rotary dryers, the dried material directly contacts the hot air, and drying is achieved through convective heat transfer. According to the flow direction of the hot air and the material, they are divided into co-current and counter-current types. The air outlet temperature in co-current dryers should generally be 10-20°C higher than the material outlet temperature, while the air outlet temperature in counter-current dryers has no specific requirement, with 100°C being a reasonable design choice. The cylinder diameter typically ranges from 0.4 to 3 meters, with a length-to-diameter ratio of 4 to 10. The circumferential speed of the dryer is 0.4 to 0.6 m/s, and the airspeed is between 1.5 to 2.5 m/s.
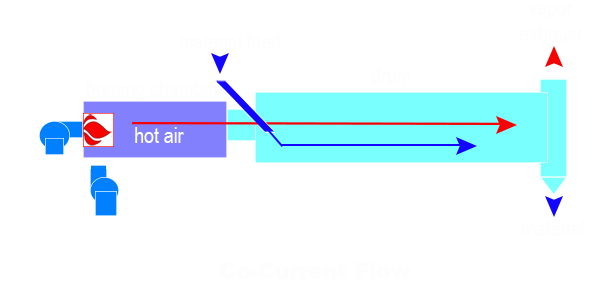
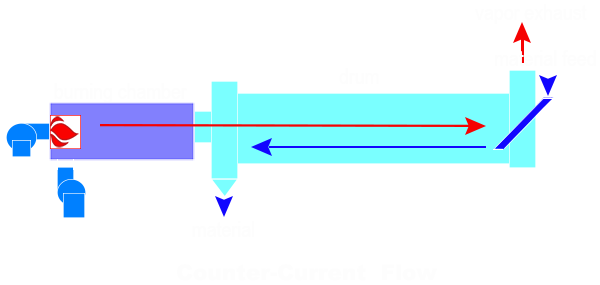
Blade-through-flow rotary dryers can be divided into end-blowing and side-blowing types based on the method of hot air injection. End-blowing types have a horizontal cylinder with many blades tilted from the entrance side to the exit side along the inner wall. Hot air enters from the bottom end, blowing through the blade gaps with the material layer to ensure thorough drying. The material moves from the entrance side to the exit side under the rotation and inclination of the blades. Side-blowing types are slightly inclined, with most hot air blowing into the cylinder from small holes along its side, perpendicular to the material’s movement direction. They have a box-shaped shell divided into 3-4 independent chambers, each with its blower, air heater, and intake/exhaust ports. This design ensures efficient contact between hot air and material, enhancing heat and mass transfer processes.
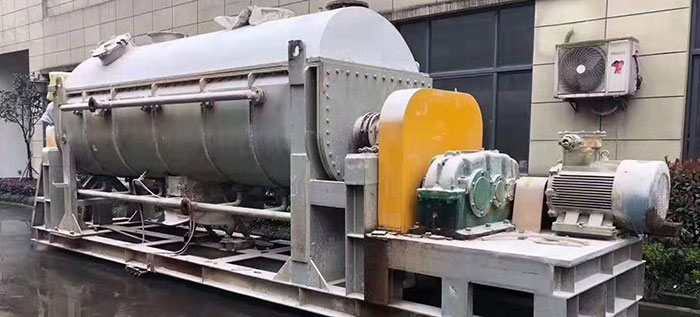
Ventilated rotary dryers have a similar design and installation to conventional types but lack paddles inside. Material moves through the bottom of the cylinder, forming a stable layer. Hot air enters through a central pipe, jetting out through small holes to contact the material. This design ensures effective contact and uniform gas distribution, doubling the volumetric heat transfer coefficient compared to conventional types, with the cylinder’s circumferential speed being about half that of conventional dryers.
Indirect Heating Rotary Dryers
In this type of dryer, the heat carrier does not directly contact the dried material, and all the drying heat is transferred through the heating wall. Indirect heating rotary dryers are divided into conventional types and steam tube types based on the heat carrier.
Conventional indirect heating rotary dryers have a cylinder built inside a furnace, heated by flue gas. A concentric cylinder is also set inside. Flue gas enters the annular space between the shell and the furnace wall and passes through connecting pipes into the central pipe inside the drying cylinder. Alternatively, flue gas enters the central pipe first, then returns to the annular space. A blower can introduce a small amount of air into the drying cylinder to remove vaporized moisture, with the air volume being significantly smaller than that of direct heating types. Due to low airspeed (typically 0.3-0.7 m/s), little dust is carried away, and gas-solid separation equipment is almost unnecessary. In many cases, natural ventilation can remove vaporized moisture without a blower.
Steam tube indirect heating rotary dryers have 1-3 rings of heating tubes arranged concentrically inside the drying cylinder. One end is connected to a drainage separation chamber, and the other end is fixed on the tube plate of a rotating head. Steam or hot water enters through a steam journal tube, distributed to each heating tube, with condensate draining out via the steam journal tube. The material is dried through the heating and agitation of the heating tubes and moves from the higher end to the lower end due to the cylinder’s inclination, discharging through an outlet hopper. This type has three times the unit volume drying capacity of conventional direct heating rotary dryers, with a heat transfer coefficient of 40-120 W/(m²·°C) and a thermal efficiency of 80-90%. The material filling rate is 0.1-0.2.
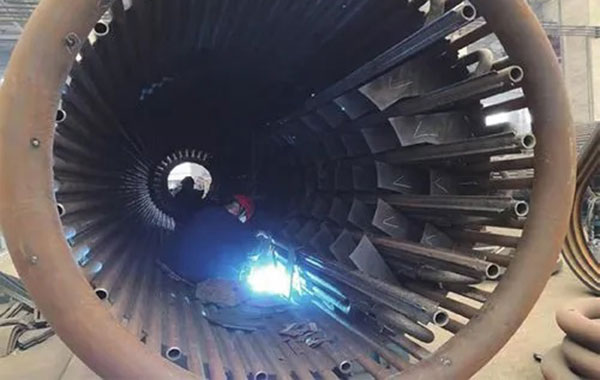
Composite Heating Rotary Drum Dryer
In this type of dryer, part of the heat is transferred to the material being dried through the heat transfer wall by the drying medium, while another part of the heat is directly transferred to the material by the heat carrier through contact. This combination of heat conduction and convection heat transfer results in high heat utilization efficiency. The dryer mainly consists of a rotary drum and a central inner tube. Hot air enters the inner tube and exits through the raw material supply end after folding into the outer tube from the material outlet end. The material moves along the annular space between the outer shell wall and the central inner tube. The necessary heat for drying is partly transferred to the material by heat conduction through the heat transfer wall of the inner tube by the hot air. The other part of the heat is transferred to the material by convection as the hot air counterflows with the material in the annular space between the outer shell wall and the central inner tube.
Steam Calcination Rotary Dryer
In the steam calcination type dryer, calcination and drying occur simultaneously. It is equipped with its own material return device. Heat is obtained through steam heating of finned tubes set inside the rotary drum. This type of dryer has a high heat transfer coefficient and an efficiency that can reach 75%, with an evaporation intensity of 50 kg (water)/m³.
Spray Granulation Rotary Dryer
This type of dryer combines drying and granulation of the product in a single rotary drum. The slurry is sprayed into the drum through nozzles. The drum interior is equipped with return screw lifters, which allow the product to return itself, thus reducing the return ratio, simplifying the process, lowering equipment load, and increasing production intensity.